Pulverbeschichtung
Inhaltsverzeichnis
1. Definition: Was ist Pulverbeschichten?
Das Pulverbeschichten ist ein modernes Beschichtungsverfahren, bei dem ein elektrostatisch aufgeladenes Lackpulver auf die behandelte Oberfläche eines leitenden Werkstoffes aufgetragen und unter Wärmeeinwirkung zu einer gleichmäßigen Farbschicht vernetzt wird. Deshalb wird das Verfahren in der Praxis häufig als Pulverlackieren bezeichnet. Da die Lackpulver auf verschiedenen Grundstoffen wie Epoxidharz, Polyesterharz oder Polyamid basieren, gibt es für nahezu jede Anwendung sowie für jeden individuellen Anspruch an Schichtaufbau, Schichtdicke, Struktur und Glanz den passenden Lack. Pulverbeschichtete Oberflächen sind langandauernd kratzfest, schlagfest, korrosions- und witterungsbeständig.
2. Technik und Verfahrensablauf: Wie funktioniert das Pulverbeschichten?
Das Pulverbeschichten untergliedert sich in drei wesentliche Teilprozesse, die bei industriellen Anwendungen durch eine automatische Förderanlage untrennbar miteinander verbunden sind. Dies bedeutet, dass die zu lackierenden Werkstücke während des gesamten Ablaufes an eigens dafür konzipierten Werkstückträgern verbleiben.
-
1. Vorbehandlung
Ziel der Vorbehandlung ist das Schaffen einer optimalen Oberfläche zur Lackapplikation. Dazu müssen die Bauteile sorgfältig von Rost, Zunder, Fett, Aufklebern, Fremdschichten, Schmutz und Staub befreit werden. Je nach Anzahl, Geometrie und Materialeigenschaften kann dies auf mechanischem oder chemischem Weg geschehen. Bei Werkstücken aus Aluminium ist zudem das Entfernen der natürlichen Oxidschicht erforderlich. Anschließend erfolgt das sogenannte Konversieren. Dabei wird durch eine chemische Reaktion des Metalls mit einer Säure, durch Phosphatieren, Eloxieren oder Chromatieren ein fester Haftgrund geschaffen. Zusätzlich verbessert dieser Vorbehandlungsschritt den späteren Korrosionsschutz. Der Vorbehandlungsprozess schließt mit dem Trockenen der Werkstücke oder der Bauteile ab.
-
2. Aufbringen (Applikation) des Lackpulvers
Das Aufbringen des Pulvers erfolgt entweder manuell oder mechanisch mithilfe spezieller Pulversprühpistolen. Diese sind so konstruiert, dass sie aus dem Lackpulver eine elektrostatisch aufgeladene Pulverwolke erzeugen. Die Werkstücke hängen einzeln angeordnet auf dem Werkstückträger. Dieser ist geerdet, sodass die Lackpartikel haften bleiben und auf der Werkstückoberfläche eine dichte Pulverschicht bilden.
-
3. Vernetzen und Trocknen
Nach dem Besprühen fahren die Werkstückträger in einen Ofen, in dem Temperaturen zwischen 120 und 250 °C herrschen. Die genaue Arbeitstemperatur und die Verweilzeit im Ofen richten sich nach der Zusammensetzung des Lackpulvers und der Werkstückdicke. Je nach Lackzusammensetzung und geforderter Eigenschaften an die spätere Oberfläche können mit dem Pulverbeschichten Schichtdicken zwischen 60 und 130 Mikrometern erzielt werden.
In allen Pulverbeschichtungsanlagen wird das überschüssige Pulver, welches nicht auf den Werkstücken „gelandet“ ist, gesammelt, aufbereitet und wiederverwendet.
3. Was sind die Vor- und Nachteile des Pulverbeschichtens gegenüber dem Nasslackieren?
Vorteile Pulverbeschichtung
Das Pulverbeschichten auf einer hochmodernen Beschichtungsanlage ist im Vergleich zum Nasslackieren nicht nur wirtschaftlicher und schneller, sondern aufgrund der Pulverzusammensetzung, des Prozessablaufes und der Wiederverwendung „danebengegangenen“ Pulvers auch umweltfreundlicher. Zudem ist das Einsatzspektrum der Pulverbeschichtung sehr breit gefächert. Hier die wesentlichen Vorteile auf einen Blick:
- keine Lösungsmittel, giftige Zusatzstoffe oder Schwermetalle
- gesundheitlich unbedenkliche Oberflächenschicht
- keine besonderen Anforderungen an die Konstruktion der Bauteile, die beschichtet werden sollen, es ist lediglich ein Loch zum Aufhängen zu berücksichtigen
- keine Einschränkungen bezüglich der Teilegröße
- keine Gefahr von „Farbnasen“ oder Tropfen
- hohe chemische und mechanische Beständigkeit
- hervorragende Witterungsbeständigkeit
- sehr gute dynamische Eigenschaften
- hohe Schichtdicken verdecken Unregelmäßigkeiten und ermöglichen homogene, optisch ansprechende Oberflächen
- wirtschaftlich, exzellentes Preis-Leistungs-Verhältnis
Nachteile Pulverbeschichtung
Die Qualität der Pulverbeschichtung wird zum Großteil durch die fachgerechte Vorbehandlung bestimmt. Diese ist vergleichsweise zeit- und arbeitsintensiv. Weitere Nachteile können sein:
- Es lassen sich aktuell nur elektrisch leitfähige und hitzeunempfindliche Materialen pulverbeschichten.
- Vor einem Farbwechsel ist die gründliche Reinigung der Sprühkabine erforderlich.
- Das Beschichten von scharfkantigen Bauteilen und Werkstücken mit kleinen Hohlräumen oder Hinterzügen ist schwierig. Aufgrund stark schwankender Feldlinienverläufe kommt es zu unerwünscht unterschiedlichen Schichtdicken (z. B. Überbeschichtung an den Kanten bei gleichzeitig unzureichender Beschichtung in den inneren Ecken).
4. Weitere Verfahrensarten
Neben der beschriebenen elektrostatischen Pulverbeschichtung, kurz EPS, gibt es mehrere Pulversinterverfahren zur Innen- und/oder Außenbeschichtung von Kleinteilen, Behältern und Rohren. Dazu gehören beispielsweise das Sintraflux-Verfahren, das Wirbelsintern und das Schüttsintern. Bei allen Sinterverfahren werden vor dem Aufbringen der Farbpulver mithilfe von Riesel- und Schüttvorrichtungen oder Rüttelkästen die zu beschichtenden Werkstücke erhitzt. Bei Berührung mit der heißen Werkstückoberfläche schmilzt das Pulver und bildet eine homogene Schicht.
5. Anwendungsgebiete der Pulverbeschichtung
Neben dem Oberflächenschutz und der Verbesserung der Optik beeinflusst das Pulverbeschichten auch die technisch funktionalen Eigenschaften der Werkstücke und Bauteile. Somit eignet sich das Verfahren beispielsweise zur Erzeugung antistatischer, salzwasserbeständiger, graffitiresistenter oder antimikrobakterieller Oberflächen.
Häufige Einsatzgebiete inklusive typischer Beispiele:
- Bauwesen: Fenster, Türen, Rollläden, Säulen, Fassaden, Geländer, Zäune
- Möbel und Haushaltsgeräte: Heizkörper, Verkleidungen von Kühlschränken und Waschmaschinen, Gehäuse von Küchengeräten aus Metall, Möbel und Möbelgestelle für Terrassen und Gärten
- Automobil- und Zweiradbau: Felgen, kleinere Bauelemente und Fahrwerksteile, die besonders vor Rost geschützt sein sollen, Fahrradgestelle und Anbauteile
- Baumaschinen, Landmaschinen, Nutzfahrzeuge: Bauelemente, Gehäuse und Verkleidungen aus Metall, die Verschleiß infolge von mechanischen Einwirkungen, Witterungseinflüssen, Baustoffen und Chemikalien ausgesetzt sind.
Welche Materialien eignen sich für das Pulverbeschichten?
Die elektrostatische Pulverbeschichtung basiert darauf, dass Teilchen, deren elektrische Ladung entgegengesetzt ist, sich einander anziehen. Darüber hinaus ist Wärme im Spiel. Deshalb ist das Verfahren für stabile, temperaturunempfindliche, elektrisch leitende Objekte geeignet. Es lassen sich praktisch alle Metalle pulverbeschichten, allen voran:
- Stahl
- Edelstahl
- feuerverzinkter Stahl
- Aluminium
Aktuell arbeiten Ingenieure und Wissenschaftler daran, auch temperaturempfindliche, nicht-leitende Werkstoffe wie Kunststoffe oder Holz zuverlässig und reproduzierbar mit einer Pulverlackierung zu versehen.
6. Fragen und Antworten zur Pulverbeschichtung
Weitere Fragen zum Thema pulverbeschichtete Oberflächen
Die häufig vertretene Meinung, dass pulverbeschichtete Teile optisch schlechter ausfallen als nasslackierte, ist ein Vorurteil. Moderne Pulverlacke ermöglichen eine riesige Farbauswahl, matte und glänzende Designs sowie das Erzeugen von Metalliceffekten. Standardfarben gemäß Classic-Farbkarte stehen ebenso zur Verfügung wie RAL-Designfarben, Sonderfarben, Neonfarben und Farben aus dem NCS-Farbsystem. Die gängigsten Farben für industrielle Anwendungen sind Schwarz, Weiß, Anthrazit. Rot, Gelb und Silber.
Standardpulver werden bei 160 bis 190 °C vernetzt (umgangssprachlich: „eingebrannt“) und haben eine Wärmebeständigkeit von bis zu 130 °C. Es gibt jedoch auch spezielle Pulverlacke auf Silikonbasis, die sich bei deutlich höheren Temperaturen vernetzen. Diese Oberflächen halten Temperaturen von 500 °C und mehr stand.
Bei einem bestimmungsgemäßen Umgang ist eine pulverbeschichtete Oberfläche sehr lange ohne Qualitätsverlust haltbar. Je nach Vorgaben und Ausführung besitzt sie eine brillante Farbe, ist extrem stoßfest, witterungsbeständig und trotzdem pflegeleicht. Die Robustheit und lange Lebensdauer spiegelt sich auch in den Garantieversprechen der Hersteller wider. Die Betreiber moderner Pulverbeschichtungsanlagen gewähren auf allgemeine Anwendungen für Innen- und Außenbereiche durchschnittlich 5 und für Spezialanwendungen bis zu 10 Jahren Garantie.
Suchen Sie weitere Möglichkeiten der Bearbeitung?
Ihre über uns produzierten Metall-Bauteile liefern wir als Rohteile oder bearbeitet, veredelt oder als Baugruppe montiert.
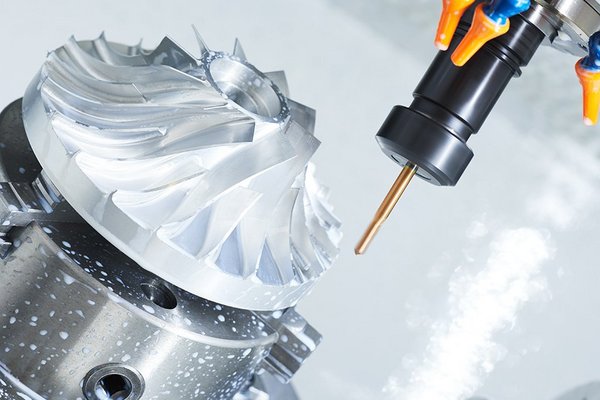
Bearbeitung / Baugruppen
Umfassende Bearbeitung, Oberflächenbehandlung von Formteilen ✓ Vormontage und Montage von Baugruppen ✓ Teilen Sie uns jetzt Ihre Anforderungen mit!
Weitere Fachbegriffe im Glossar:
- Baugruppen
- Bräunling (MIM Verfahren)
- Dampf-Autoklav
- DIN ISO
- Elektropolieren
- Eloxieren / Eloxal-Verfahren
- Entbinderung (MIM-Verfahren)
- Feedstock (Granulat)
- Formschlicker (Feingussverfahren)
- Gesenk
- Grünling (MIM-Verfahren)
- ISO 14001:2015
- ISO 9001:2015
- Kerbschlagzähigkeit
- KTL-Beschichtung
- Legierung in der Metallurgie
- Magnetpulverprüfung / Fluxen
- Materialverlust
- Metallische Werkstoffe
- Passivieren
- Prototyp
- Pulverbeschichtung
- Reproduzierbarkeit
- Rohling (Werkstück)
- Strahlen
- Verzinken: das Verzinkungsverfahren
- Vorfinanzierung
- Wachsbaum (Feingussverfahren)
- Wachsmodell (Feingussverfahren)
- Wachsspritzwerkzeug (Feingussverfahren)
- Zugfestigkeit
- Zunderschicht