Elektropolieren – Elektropolitur
Inhaltsverzeichnis
1. Definition Elektropolieren – Elektropolitur
Elektropolieren, häufig auch Elektropolitur oder elektrolytisches Polieren genannt, ist ein elektrochemisches Verfahren zur Behandlung metallischer Oberflächen ohne thermische oder mechanische Belastung. Zwischen dem Metallbauteil und einem flüssigen Elektrolyten erfolgt ein elektrischer Ladungsaustausch, in dessen Folge Teilchen im Mikrobereich von der Bauteiloberfläche abgetragen werden. Die Elektropolitur führt zum Einebnen, Passivieren und zur Veredelung ursprünglich rauer, matter metallischer Oberflächen, die nach der Behandlung glänzen.
Das Prinzip des Elektropolierens ist ein umgekehrter galvanischer Prozess und gehört gemäß DIN 8590 zu den elektrochemisch abtragenden Fertigungsverfahren.
2. Wie funktioniert das Elektropolieren? Beschreibung des Elektropolitur-Verfahrens
Elektropolieranlagen bestehen aus beheizbaren Tauchbädern, Stromarmaturen mit stufenlos einstellbaren Gleichrichtern und Aggregaten zur Kühlung. Das Herzstück einer jeden Anlage ist das Polierbecken, in dem sich eine hoch konzentrierte Säuremischung befindet. Die genaue Zusammensetzung dieser Mischung und damit des Elektrolytbades richtet sich nach dem Werkstoff und der Beschaffenheit des Werkstückes, welches elektropoliert werden soll. Das Elektropolieren von Edelstahl beispielsweise erfolgt in einem Bad, welches aus einem hoch konzentrierten Schwefelsäure-Phosphorsäure-Gemisch mit Zusätzen besteht, die den Wirkungsgrad, das Einebnen von Rauheiten und den Glanz verbessern. Im stromlosen Zustand greift das Elektrolytgemisch die Edelstahloberfläche nicht an.
Das zu bearbeitende Bauteil wird an einem Gestell aus Bronze, Kupfer oder Titan befestigt, an den Pluspol einer Gleichstromquelle angeschlossen und in das Elektrolytbad eingetaucht. Nach Einschalten des Gleichstromes fungiert die elektrolytische Flüssigkeit als Leiter (Anode). Unter Einwirkung des Stromes lösen sich kleinste Teile an der Metalloberfläche auf. Das führt zur Beseitigung von Rauigkeiten, sodass im Ergebnis eine metallurgisch reine, passivierte, blank glänzende Oberfläche entsteht. Da unter dem Einfluss des Gleichstromes auch mikrofeine Strukturen an den Ecken und Kanten abgebaut werden, eignet sich die Elektropolitur überdies hervorragend zur Feinentgratung.
Eine wesentliche Voraussetzung für das Erzielen einwandfreier Ergebnisse ist eine sehr gründliche Vorbehandlung und Reinigung der elektrolytisch zu polierenden Bauteile. Vor allem Zunder, Fett und Farbreste sind vor dem Elektropolieren sorgfältig zu entfernen, da die Metalloberfläche ansonsten nicht gleichmäßig vom Elektrolyten erfasst werden kann. Auch mechanische Beschädigungen wirken sich auf das Ergebnis ungünstig aus, da sie durch den verfahrensbedingt stärkeren Materialabtrag an Ecken und Kanten nach der Elektropolitur deutlich sichtbarer werden.
Nach dem Entfernen aus dem Tauchbad müssen die polierten Teile unter fließendem Wasser gründlich gespült werden. Zum rückstandslosen Ablösen sämtlicher Elektrolytreste sind je nach Größe und Bauteilgeometrie zumeist mehrere Spülgänge erforderlich.
In Abhängigkeit vom Aufwand in Bezug auf die Vor- und Nachbehandlung dauert ein Elektropoliervorgang zwischen fünf und 20 Minuten.
3. Welche Materialien lassen sich elektropolieren?
Prinzipiell eignet sich das Oberflächenveredlungsverfahren für alle rostfreien Stähle. Ausnahmen bilden allerdings Stähle, die mit Niob oder Titan stabilisiert sind. Diese eignen sich für die Elektropolitur aufgrund der beständigen Niob- und Titancarbonitride nicht. Auch Aluminium, Messing und Kupfer können in einer Elektropolieranlage sehr gut bearbeitet werden.
Für den optimalen Poliereffekt ist stets der Materialzustand des Werkstückes in Verbindung mit der Oberflächenbeschaffenheit entscheidend. Zugleich beeinflussen die Bestandteile der Legierung und die vorherige Materialbehandlung wie beispielsweise das Härten während der Fertigung den elektrolytischen Materialabtrag. In der Praxis lässt sich die Eignung bestimmter Materialien und Oberflächen deshalb häufig nur durch gezielte Versuche ermitteln.
4. Folgende Voraussetzungen müssen Werkstücke beim Elektropolieren erfüllen:
- elektrisch sehr gut leitende Oberfläche
- mechanisch einwandfrei vorgearbeitete Oberfläche
- günstige Werkstückgeometrie
- bei Massenteilen gute Schüttfähigkeit
- ausreichend dicke Wandstärken
- geeignete Kontaktstellen zum Anlegen des Gleichstromes.
Walzfehler, Einlagerungen elektrolytisch nicht polierbarer Materialstrukturen, mechanische Beschädigungen und dergleichen lassen sich mit dem Elektropolieren nicht ausgleichen. Die Elektropolitur ist immer eine Feinbearbeitung sorgfältig mechanisch vorbehandelter metallischer Oberflächen.
5. Technische Anwendung des Elektropolierens und der elektrolytischen Feinentgratung
Grundsätzlich kommt das elektrochemische Fertigungsverfahren zur Oberflächenfeinbearbeitung von Stanz-, Dreh- und Frästeilen zum Einsatz. Die prozessgesteuerte Elektropolitur garantiert vor allem für produktberührte Flächen optimale Oberflächenzustände. Die Bandbreite reicht von funktionalen Oberflächen mit bestimmten Zielrauheitswerten bis hin zu rein optisch attraktiv glänzenden Sichtflächen. Die zu erzielende Oberflächenbeschaffenheit und die damit verbundene Materialabtragung werden in der Praxis durch eine exakte Oberflächenspezifikation definiert.
Für die Wirksamkeit des Elektropolierens im Hinblick auf die Feinentgratung sind das Verhältnis der vorhandenen Grate zur Form und Größe des Werkstücks von Bedeutung. Grate mit einer großen Oberfläche und einem schmalen Gratfuß im Verhältnis zur Masse wie beispielsweise Schleifgrate, lassen sich durch Elektropolieren besser entfernen als Grate mit ausgeprägtem Graßfuß. Bei entsprechender mechanischer Vorentgratung stellt jedoch auch hier die elektrolytische Feinbehandlung eine wirtschaftliche Lösung dar.
6. Typische Einsatzbeispiele für elektropolierte Teile sind:
- Medizin- und Pharmatechnik: Chirurgische Instrumente, Krankenhausausstattung sowie Gegenstände, die Ionenstrahlung ausgesetzt sind oder mikrobiologischen Kontaminierungen unterliegen.
- Nahrungs- und Genussmittelindustrie: Geräte zur Wasseraufbereitung, Oberflächen, die vor der Ansiedelung von Bakterien, Keimen, Pilzen etc. geschützt werden müssen.
- Städtebau: An elektropolierten Outdoormöbeln, Spiel- und Sportgeräten haftet kaum Schmutz an. Graffiti lässt sich leicht entfernen.
Durch den Einsatz von moderner Gleichrichtertechnik in Verbindung mit der optimalen Elektrolytzusammensetzung lassen sich mit dem elektrolytischen Polieren hohe Prozesssicherheiten sowie reproduzierbare Ergebnisse bezüglich der erforderlichen Oberflächen erzielen.
7. Vorteile des Elektropolierens auf einen Blick
Verbesserung der Optik
Hohe Reflexionswerte und der damit verbundene Glanz bewirken eine Verbesserung der Optik.
Entgratungseffekt
Abrundung scharfer Kanten.
Abbau von Spannungen
Abbau mechanischer und thermischer Spannungen in der Metalloberfläche.
Keine Poliermittelrückstände
Rückstandsfreie, metallisch reine Oberfläche.
Höhere Korrosionsbeständigkeit
Dank deutlich stärkerer Passivschicht ist elektropolierter Edelstahl korrosionsbeständiger.
Glattere Oberfläche
Elektropolieren wirkt sich wesentlich auf die Rauheit aus. Die Oberfläche wird glatter, was beispielsweise in Reaktoren oder Rohrleitungen das Strömungsverhalten von Fluiden verbessert. Keime und andere unerwünschte Substanzen können sich nur schwer festsetzen.
Höhere Keimresistenz
Elektrolytisch polierte Oberflächen sind bis zu einem bestimmten Grad keimresistent. Sie lassen sich einfach reinigen und desinfizieren.
Gleichmäßige Anwendung
Auch Teile mit sehr komplexen Formen und Aussparungen werden gleichmäßig poliert.
Vorteile für Kleinteile
Für Kleinteile ist die Elektropolitur schneller, effektiver und damit kostengünstiger als mechanische Fertigungsverfahren.
Niedrigen Reibungskoeffizienten
Zudem punkten elektropolierte Oberflächen mit extrem niedrigen Reibungskoeffizienten, was beispielsweise bei Verschleißteilen von großer wirtschaftlicher Bedeutung ist.
Suchen Sie weitere Möglichkeiten der Bearbeitung?
Ihre über uns produzierten Metall-Bauteile liefern wir als Rohteile oder bearbeitet, veredelt oder als Baugruppe montiert.
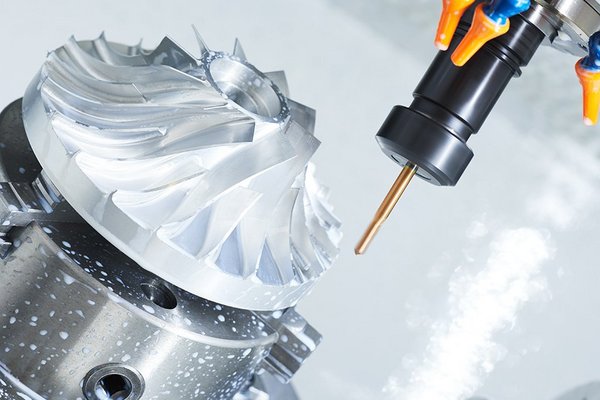
Bearbeitung / Baugruppen
Umfassende Bearbeitung, Oberflächenbehandlung von Formteilen ✓ Vormontage und Montage von Baugruppen ✓ Teilen Sie uns jetzt Ihre Anforderungen mit!
Weitere Fachbegriffe im Glossar:
- Baugruppen
- Bräunling (MIM Verfahren)
- Dampf-Autoklav
- DIN ISO
- Elektropolieren
- Eloxieren / Eloxal-Verfahren
- Entbinderung (MIM-Verfahren)
- Feedstock (Granulat)
- Formschlicker (Feingussverfahren)
- Gesenk
- Grünling (MIM-Verfahren)
- ISO 14001:2015
- ISO 9001:2015
- Kerbschlagzähigkeit
- KTL-Beschichtung
- Legierung in der Metallurgie
- Magnetpulverprüfung / Fluxen
- Materialverlust
- Metallische Werkstoffe
- Passivieren
- Prototyp
- Pulverbeschichtung
- Reproduzierbarkeit
- Rohling (Werkstück)
- Strahlen
- Verzinken: das Verzinkungsverfahren
- Vorfinanzierung
- Wachsbaum (Feingussverfahren)
- Wachsmodell (Feingussverfahren)
- Wachsspritzwerkzeug (Feingussverfahren)
- Zugfestigkeit
- Zunderschicht