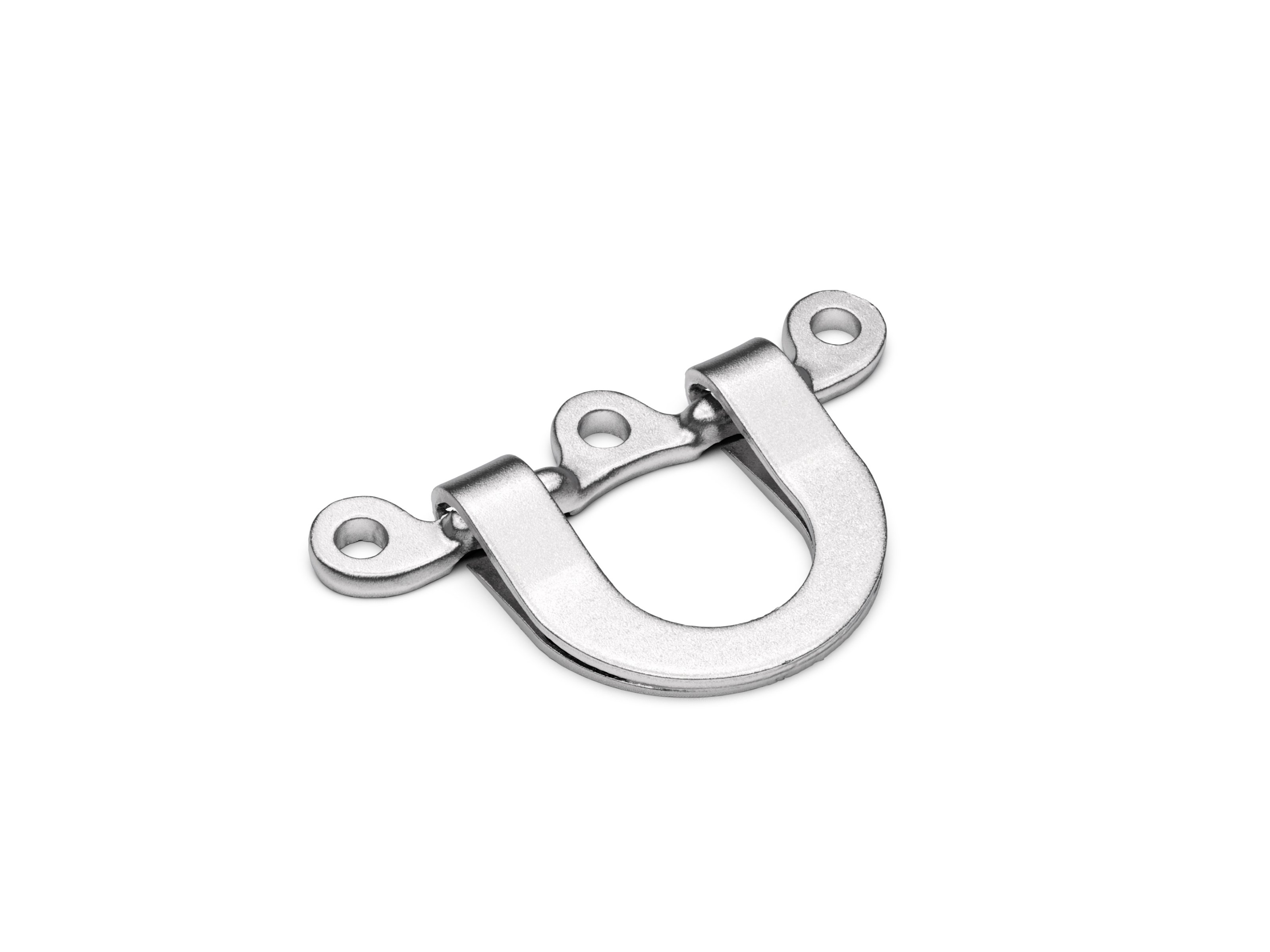
Gesenkschmieden Verfahren
Inhaltsverzeichnis
1. Was ist eine Gesenkschmiede?
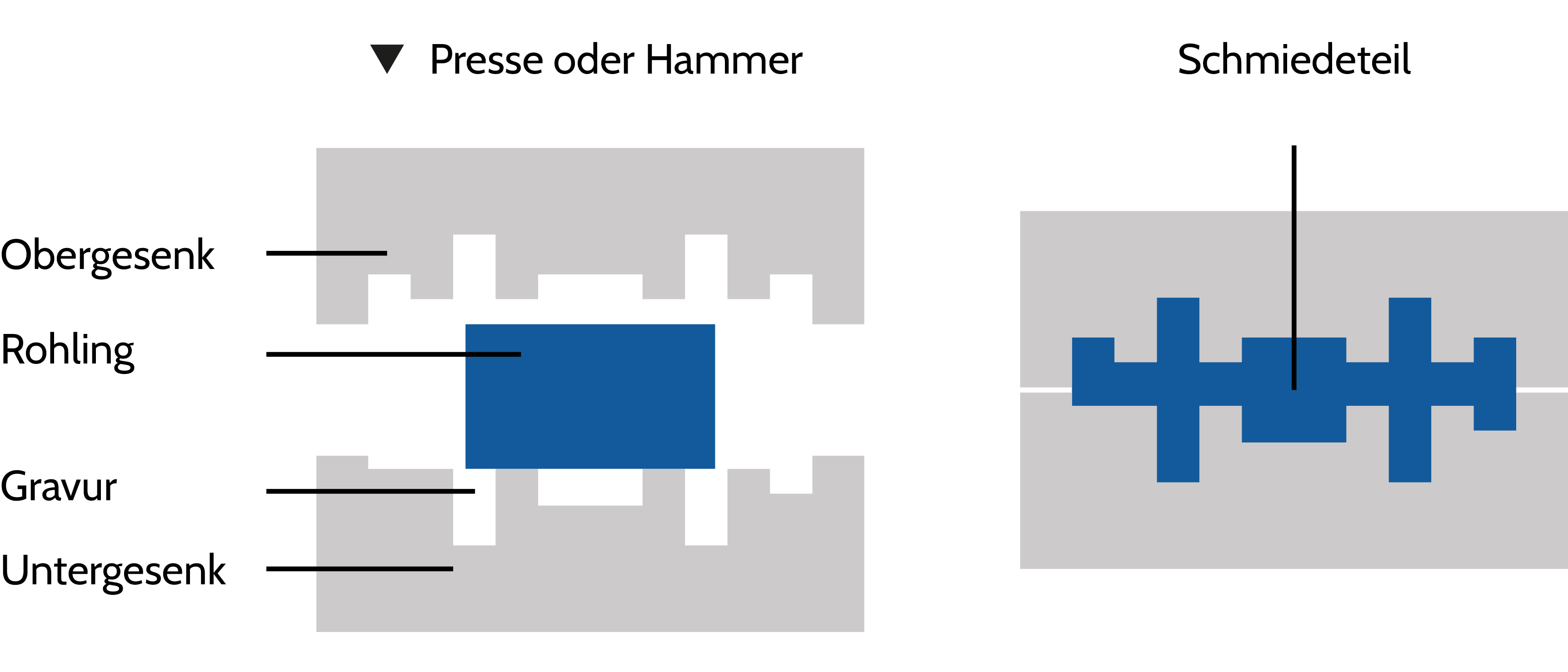
Gesenkschmieden oder auch Gesenkformen ist ein Fertigungsverfahren, genauer Umformverfahren oder Massivumformverfahren, und stammt aus der Hauptgruppe des Umformens. Dort wird es gemeinsam mit dem Walzen, Freiformen, Eindrücken und Durchdrücken der Gruppe des Druckumformens zugeordnet. Nach DIN 8583 ist es ein Druckumformen, bei dem sich Formwerkzeuge gegeneinander bewegen, die Gesenke.
Das Werkzeug enthält die Gravur des zu fertigenden Formteils als Negativ und besteht aus einem Ober- und Untergesenk. Die Gesenke werden mit großer Kraft unter Einwirkung einer Presse oder eines Hammers gegeneinander bewegt und so der Werkstoff in die gewünschte Form gearbeitet.
Die Schmiedestücke überzeugen mit einem homogenen, dichten Faserverlauf, welcher weder Poren noch anderweitige Hohlräume aufweist.
Grundsätzlich handelt es sich beim Gesenkschmieden um die am meisten verwendete Schmiedemethode. Sie kommt zum Einsatz, um zum Beispiel Flugzeug-, Schiffs- oder Autoteile herzustellen sowie bei Konstruktionen und zur Herstellung unterschiedlicher Industrieprodukte.
1.1 Gesenkformen
Das Gesenkformen zeichnet sich im Wesentlichen durch die Unterscheidung in Gesenkschmieden mit Grat und Gesenkschmieden ohne Grat aus. Beide Formen gehören zur Gruppe des Gesenkformens mit ganz umschlossenem Werkstück.
Beim Gesenkschmieden mit Grat wird der überschüssige Werkstoff in den Gratspalt der Gravur gedrängt; der sog. Grat. Das Entgraten, also das Entfernen des überschüssigen Materials, wird mit Hilfe von weiteren Werkzeugen durchgeführt, die dabei wie eine Art Stanze fungieren.
Beim Schmieden im geschlossenen Gesenk befindet sich die Gravur in einer Hälfte des Gesenkes und die zweite Hälfte geht in die erste ein. Eine Gratbildung ist in diesem Fall nicht vorgesehen, deshalb nennt man diese Art des Gesenkschmiedens auch „gratloses Schmieden“. Da kein Grat entsteht, zeichnet sich dieses Präzisionsschmiden im Besonderen durch keinen oder einen sehr geringen Materialüberschuss aus. Das Herauslösen des Formteils erfordert allerdings einen besonders hohen Kraftaufwand im Schmiedeprozess.
Neben dem gerade erwähnten Gesenkschmieden mit ganz umschlossenem Werkstück lässt sich das Gesenkformen folglich auch in Gesenkschmieden mit teilweise umschlossenem Werkstück unterteilen.
1.2 Unterteilungsformen des Gesenkschmiedens
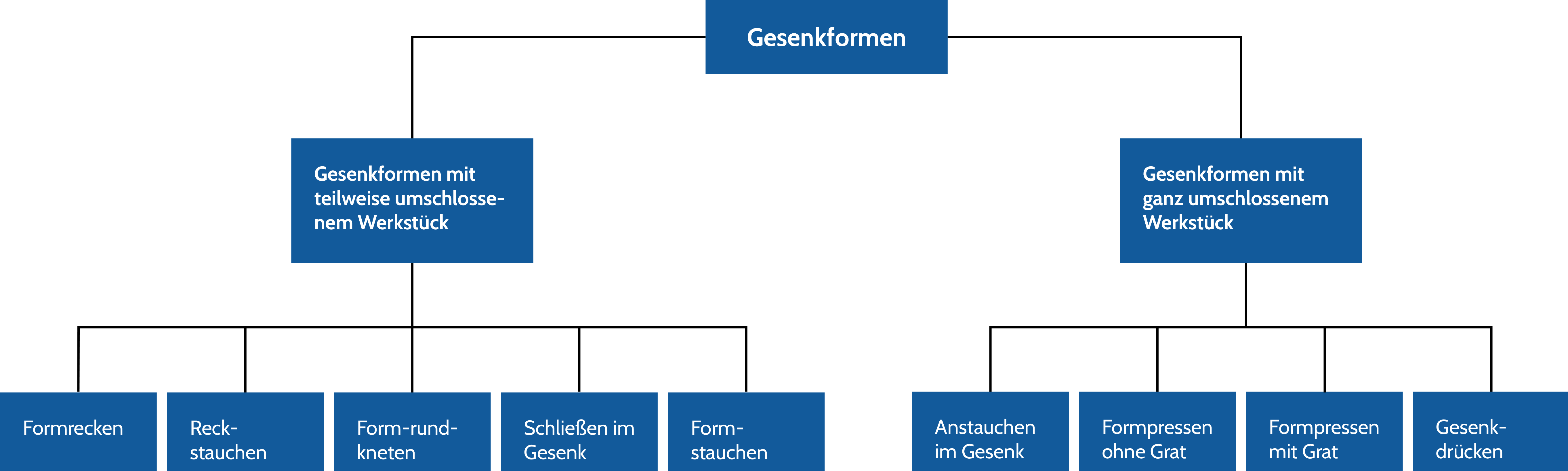
Gesenkschmieden "von der Stange"
Dem Gesenkformen mit teilweise umschlossenem Werkstück wird das Schmieden von der Stange zugeordnet. In der Regel kommen hier etwa 2 m lange Walzstangen zum Einsatz, die an einem Ende erwärmt, im Gesenk geschmiedet und im Anschluss das Werkstück von der Stange durch einen Hammerschlag getrennt werden.
Der Vorteil des Gesenkschmiedens von der Stange liegt im einfachen Handling, da das Werkstück nicht eingespannt werden muss. Jedoch ist der Werkstoffeinsatz höher, was als Nachteil anzuführen ist. Dieses Verfahren kommt dann zum Einsatz, wenn Werkstücke in einer langgestreckten Form von einem Gewicht bis zu 3 kg und Stangendurchmessern von bis zu 50 mm geschmiedet werden sollen.
Unterformen des Gesenkformens mit teilweise geschlossenem Werkstück sind das Formrecken, das Reckstauchen, das Formrundkneten, das Schließen im Gesenk und das Formstauchen.
Schmieden "vom Stück"
Beim Schmieden vom Stück handelt es sich um Gesenkformen mit ganz umschlossenem Werkstück. Hier wird entweder ein abgescherter oder abgesägter Stangenabschnitt als Ausgangsrohling verwendet. Vorteilhaft am Gesenkschmieden vom Stück ist, dass der Faserverlauf der äußeren Kontur optimal folgt. Als Nachteil kann der größere Materialeinsatz angesehen werden.
Das Gesenkschmieden vom Stück kann entweder mit oder ohne Grat erfolgen. Das Gesenkschmieden mit Grat ist in der industriellen Praxis dasjenige Formgebungsverfahren, das vorrangig zum Einsatz kommt.
In Bezug auf das Füllen der Gesenkgravuren wird zwischen drei Grundtypen von Füllvorgängen differenziert:
- Stauchen: Der Werkstofffluss verläuft hauptsächlich parallel zur Werkzeugbewegung.
- Breiten: Der Werkstofffluss verläuft hauptsächlich senkrecht zur Werkzeugbewegung.
- Steigen: Der Werkstofffluss verläuft parallel gegen die Werkzeugbewegung.
Anders als beim Schmieden mit Grat wird das Werkstück beim Schmieden ohne Grat vollständig vom Werkzeug umschlossen, entsprechend tritt kein Werkstoff aus. Der weitere Verlauf der Umformung erfolgt analog zu demjenigen mit Grat.
Schmieden "vom Spaltstück"
Das Schmieden vom Spaltstück lässt sich letztlich beiden Gesenkformen, mit ganz und teilweise umschlossenem Gesenk, zuordnen.
Das Gesenkschmieden vom Spaltstück basiert auf einer Ausgangsform, die aus einem Streifen Blech ausgeschnitten wird, wobei dieser Prozess durch Flächenschluss erfolgt und die Blechstreifen nahezu verlustlos zugeschnitten werden. Durch Biegen oder Stauchen wird eine Zwischenform erzeugt und die endgültige Form erhält das Werkstück anschließend im Gesenk.
Das Gesenkschmieden vom Spaltstück ist vorrangig für flache und kleine Werkstücke geeignet, wobei der klare Vorteil beim geringen Werkstoffverbrauch und den kurzen Schmiedezeiten liegt. Nachteilig ist der Faserverlauf, der nicht ideal an der Form des Werkstücks angepasst werden kann, wozu es zur Beeinträchtigung der Biegewechselfestigkeit kommen kann.
Dieses Verfahren kommt vor allem bei Massenteilen wie Schraubenschlüssel, Zangen, Scheren oder Messer zum Einsatz, die keiner allzu hohen Festigkeitsbeanspruchung genügen müssen.
1.3 Unterscheidung: Warm-, Halbwarm- und Kaltumformung in der Produktion
In der Produktion wird zwischen der Warm-, Halbwarm- und Kaltumformung unterschieden. Meistens erfolgt das Gesenkformen bei Werkstücktemperaturen oberhalb der Rekristallisationstemperatur, weshalb es auch als Warmumformen bezeichnet wird. Hier wird das Werkstück im Ofen auf die erforderliche Schmiedetemperatur erwärmt so dass das Metall weich wird. Dies erlaub die Herstellung von Schmiedeteilen kompliziertester Formen: Radträger, Kurbelwellen, Lenkschenkel, Pleuel, Zahnräder, Turbinenschaufeln usw..
Zum Einsatz beim Gesenkschmieden eignen sich grundsätzlich alle nach Erwärmung knetbaren Metalle. Die meisten Gesenkschmiedestücke werden zwar nach wie vor aus
Stählen hergestellt, jedoch gewinnt Aluminium als Leichtmetall oder weitere Bundmetalle immer mehr an Bedeutung. So wird das Aluminium-Schmieden gerne in der Automobilindustrie eingesetzt.
Mit der Kaltumformung im Gesenk werden präzise und hochwertige Teile hergestellt. Da das Werkstück nicht vorbereitend einer Erwärmung unterzogen wird, resultieren keine Temperaturausdehnung, Verzunderung und thermische Defekte. Trotzdem wird die Kaltumformung im Gesenk seltener verwendet, weil die meisten Metallen und ihre Legierungen im Kaltzustand eine hohe Festigkeit aufweisen und für ihre Deformation Maschinen mit sehr hoher Leistung notwendig sind.
2. Vorgänge des Gesenkschmiedens
Das Füllen der Gesenkgravur innerhalb des Gesenkschmiedens erfolgt nach den drei Grundvorgängen der geführten Werkstoffverdrängung, von denen mindestens zwei während eines Gesenkschmiedevorgangs auftreten:
- Beim Stauchen erfolgt der wesentliche Werkstofffluss parallel zur Bewegung des Werkzeuges, die Ausgangshöhe wird vermindert.
- Beim Breiten wird der Werkstoff seitlich verdrängt, wobei dies von innen nach außen geschieht. Der wesentliche Werkstofffluss findet beim Breiten senkrecht zur Bewegung des Werkzeuges statt.
- Beim Steigen werden tiefe Gravur-Hohlräume ausgefüllt, wobei der wesentliche Werkstofffluss parallel gegen die Bewegung des Werkzeuges erfolgt.
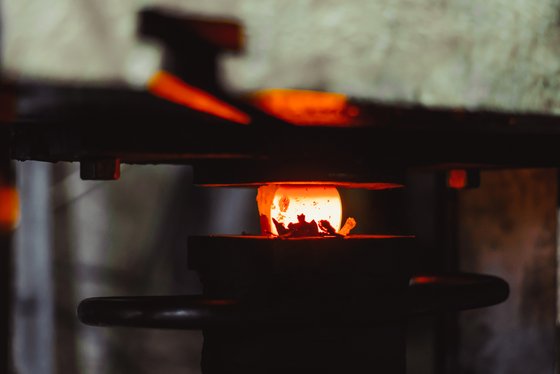
Die Übergänge der Werkstoffverdrängung erfolgen meist fließend. Auf das Werkstück wirkt eine Druckspannung, die von dem Ober- und Unterwerkzeug (oder Ober- und Untergesenk) erzeugt wird. Genauer gesagt wird dieser Druck von einer Umformmaschine, der Presse, ausgelöst (siehe Bild 1).
Die umzuformenden Bauteile werden im Vorfeld erwärmt, um die Druckspannungen und die Belastungen auf den Werkzeugen nicht zu stark werden zu lassen. Generell lassen sich nahezu alle umformbaren Materialien im Gesenk schmieden.
Stahl wird zur Umformung der Bauteile in der Regel auf 1.000 °C bis 1.280 °C erwärmt. Es können darüber hinaus auch Werkstoffe wie Magnesium, Aluminium, Edelstahl sowie Messing, Kupfer und ihre Legierungen zum Gesenkschmieden verwendet werden.
3. Ablauf beim Gesenkschmieden
1. Die Erwärmung
2. Die Umformung
3. Das Schmieden
4. Das Abgraten, Lochen und Nachformen
5. Die Wärmebehandlung/ das Vergüten
6. Das Entzundern
7. Die Endkontrolle
4. Video: Schritte beim Gesenkschmieden
5. Vorteile und Nachteile
Vorteile des Gesenkschmiedens
Beim Walzen des Vormaterials oder beim Gesenkschmieden selbst werden Fehlstellen wie Poren und Lunker geschlossen, die bei der Fertigung von Gussteilen häufig auftreten. Dadurch wird bei Schmiedeteilen, im Vergleich zu Gussteilen, eine höhere Festigkeit bei gleichem oder sogar geringerem Gewicht erwirkt.
Gegenüber zerspanten Bauteilen zeigen Schmiedeteile einen an die Umformung angepassten Faserverlauf. D.h. beim zerspanten Bauteil wird der Faserverlauf gebrochen (vgl. Bild 5). Daraus resultiert eine hohe statische und dynamische Belastbarkeit von Gesenkschmiedeteilen, da sie perfekt an ihre Beanspruchungen angepasst werden können.
Nachteile des Gesenkschmiedens
Die Art des gewählten Verfahrens bestimmt die Nachteile des Gesenkschmiedens. Die aufwendige Gesenkkonstruktion sowie der erforderliche Materialüberschuss für die Ausformung treten beim Gesenkschmieden mit Grat auf.
Beim Gesenkschmieden ohne Grat verursacht die notwendige Präzision Nachteile, da die Konstruktion der Gesenke noch aufwendiger als beim Gesenkschmieden mit Grat ist. Auch die Einhaltung sehr geringer Toleranzen innerhalb des Prozesses verursachen einen hohen Aufwand. Gesenküberlastungen durch Volumenschwankungen der Vorprodukte führen rasch zu Werkzeugversagen oder zu einer nicht vollständig gefüllten Gravur. Für die Fertigung von Werkstücken mit einer komplizierten Geometrie ist diese Fertigungsmethode nicht geeignet.
6. Faserverlauf beim Schmieden im Vergleich zu alternativen Verfahren
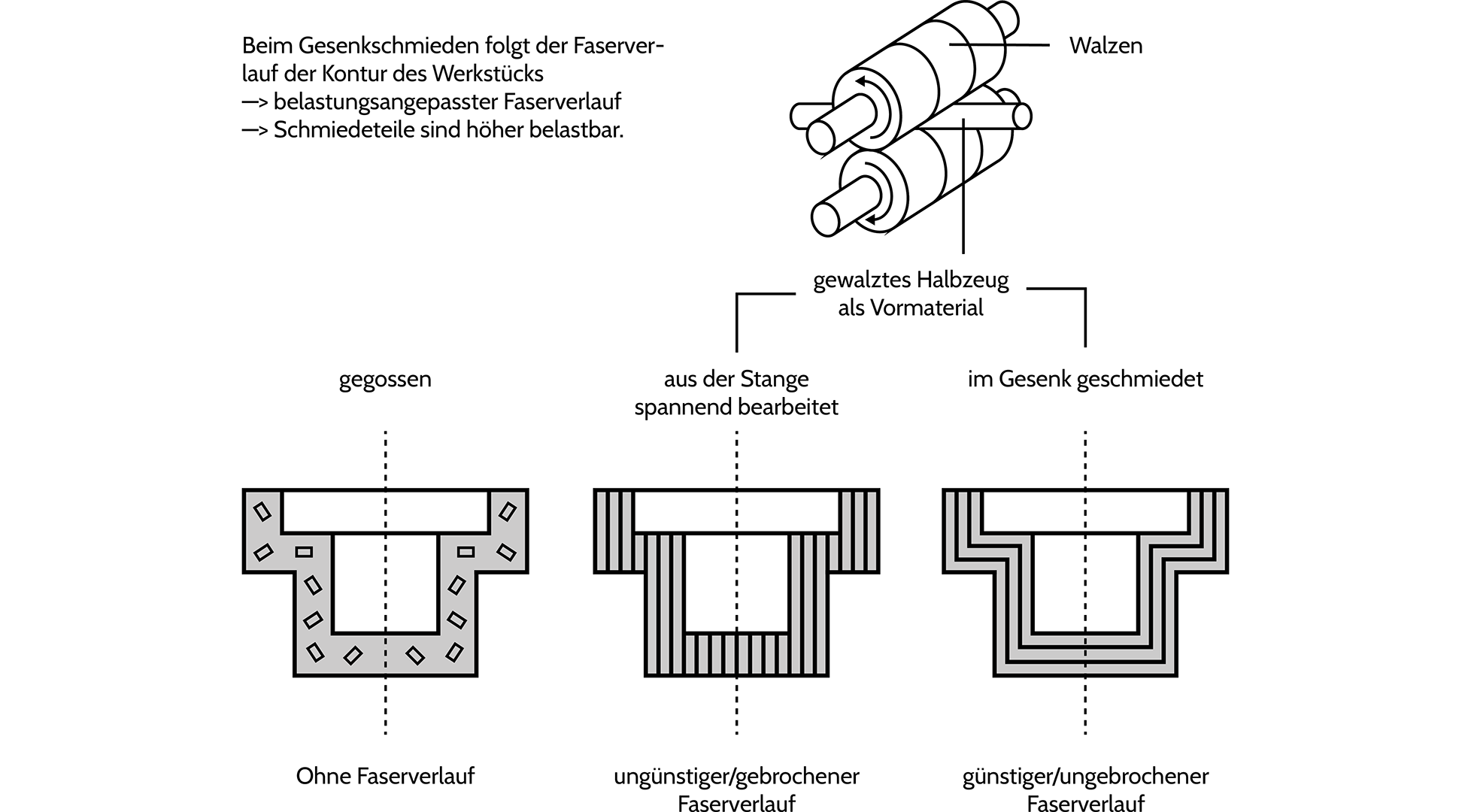
7. Ursprung und Geschichte
Das Schmiedeverfahren findet bereits seit 1.500 v. Chr. Anwendung. Damals wurde beim Gesenkschmieden der Rohling in das Gesenk gelegt und mit einem Hammer in Form geschlagen. Obwohl die Umformtechnik in den nachfolgenden Jahren fortlaufend weiterentwickelt wurde, gelang die Herstellung moderner Gesenkschmiedewerkzeuge erst gegen Ende des 19. Jahrhunderts in England.
Dieser Fortschritt wurde dabei maßgeblich von der Entwicklung des Dampfhammers begünstigt, wodurch nun auch große Teile geschmiedet werden konnten. Mit dem Voranschreiten des 20. Jahrhunderts wurde auch die erreichbare Genauigkeit im Gesenkschmieden immer höher. Moderne Entwicklungen zielen ebenfalls auf einen höheren Automatisierungsgrad des Schmiedeverfahrens ab.
8. Vielfältige Anwendungsbereiche
Das Gesenkschmieden eignet sich zum Einsatz in der Massenproduktion von einzelnen Werkstücken, wobei diese einige Gramm oder aber mehrere Tonnen wiegen können. Auch bzgl. der Maße und Seriengrößen ist eine große Bandbreite möglich: von wenigen Zentimetern bis mehrere Meter, bzw. von lediglich einigen Stücken bis zu mehreren Millionen.
Das Gesenkschmieden eignet sich zur Herstellung von Konstruktionsteilen für Maschinen wie beispielsweise Flugzeuge oder Fahrzeuge. Es wird aber auch genutzt um Werkzeuge wie Schraubenschlüssel, Zangen oder Hämmer zu produzieren.
Die Automobilindustrie, die Zweiradindustrie, der Maschinenbau sowie die Bahnindustrie, der Bergbau, der Schiffsbau und die Flugzeugindustrie sind die Hauptabnehmer in Deutschland für Werkstücke, die aus dem Gesenkschmieden hervorgehen.
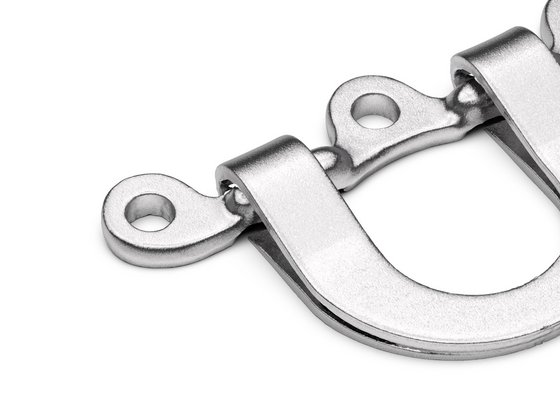
Sie benötigen Gesenkschmiede-Teile?
Informieren Sie sich hier über die Spezifika des Gesenkschmiede-Verfahrens bei Richter Formteile.
Service - ganz nach Ihrem Bedarf
Wir verstehen uns als Ihr Partner über die Wertschöpfungskette hinweg.
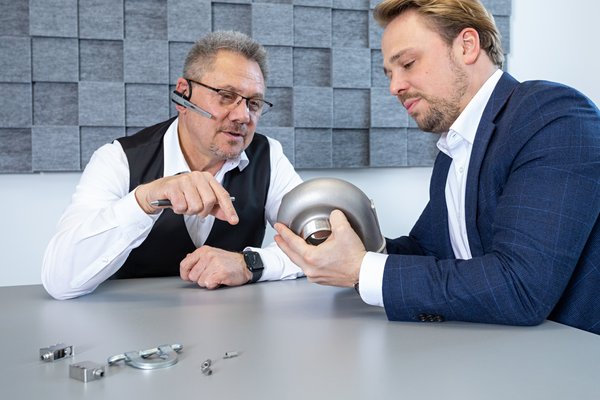
Technische Beratung
Gerne unterstützen wir Sie bei fachlichen Fragen ✓ Stimmen Sie Ihre Anforderungen und die technische Zeichnungen mit unserem Fachpersonal ab!
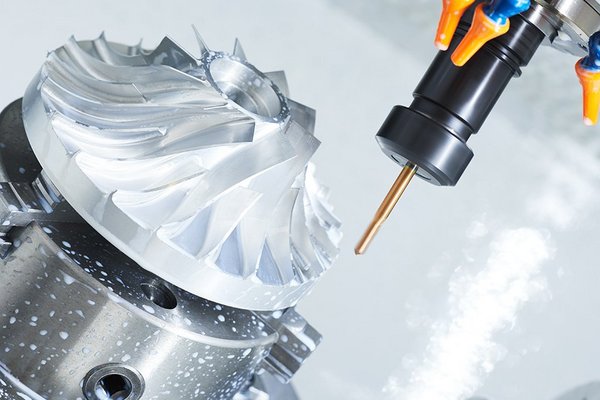
Bearbeitung / Baugruppen
Umfassende Bearbeitung, Oberflächenbehandlung von Formteilen ✓ Vormontage und Montage von Baugruppen ✓ Teilen Sie uns jetzt Ihre Anforderungen mit!
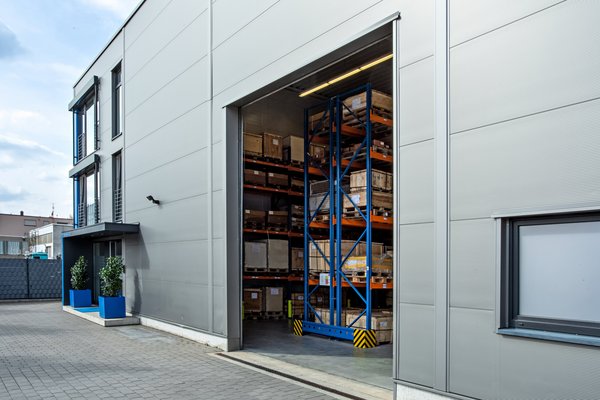
Supply Chain Management
Wir kümmern uns neben der Entwicklung und Produktion der Bauteile auch um ✓ Beschaffung ✓ Logistik ✓ Verzollung - Jetzt informieren und Vorteile nutzen!
Wir sind in allen Branchen zu Hause
Wir sind in der Branche zuhause, wo unsere Kunden sind. Erfahren Sie hier mehr zu unseren Referenzen.
Antriebstechnik
Armaturen und Pumpen
Bauindustrie
Elektroindustrie
Fahrzeugbau
Filtertechnik
Land- und Forstwirtschaft
Lebensmittelindustrie
Maschinenbau
Medizintechnik
9. Fragen und Antworten rund um das Thema Gesenkschmieden
FAQs zum Gesenkschmieden
In einer Gesenkschmiede wird das Gesenkschmieden als Fertigungsverfahren genutzt. Dabei wird ein erhitztes Metallstück (meist Stahl, Aluminium oder Messing) zwischen zwei speziell geformten Gesenken (Werkzeugformen) gepresst, um es in eine gewünschte Form zu bringen.
Merkmale des Gesenkschmiedens:
- Hohe Präzision: Durch das Gesenk entsteht eine exakte, wiederholbare Form.
- Hohe Festigkeit: Das Schmieden verbessert die Materialeigenschaften, da das Gefüge verdichtet und Fasern in die gewünschte Richtung ausgerichtet werden.
- Serienproduktion: Ideal für die Herstellung großer Stückzahlen, z. B. für Automobil-, Maschinenbau- oder Luftfahrtteile.
- Verschiedene Verfahren: Es gibt Warm-, Halbwarm- und Kaltschmieden, wobei Warm- und Halbwarmverfahren am häufigsten genutzt werden.
Anwendungen:
- Kurbelwellen
- Pleuelstangen
- Zahnräder
- Werkzeuge (z. B. Schraubenschlüssel, Hämmer)
- Fahrwerkskomponenten in der Automobilindustrie
Gesenkschmieden ist ein wichtiger Prozess in der Metallverarbeitung, da es robuste und hochbelastbare Bauteile ermöglicht.
Gesenkschmieden ist ein umformendes Fertigungsverfahren, bei dem ein erhitztes Metallstück (meist Stahl, Aluminium oder Messing) zwischen zwei Gesenken in eine bestimmte Form gepresst wird. Die Gesenke sind spezielle Werkzeuge mit einer Hohlform, die das Werkstück beim Schmieden in die gewünschte Geometrie bringen.
Dieses Verfahren wird genutzt, um hochfeste und präzise Bauteile für verschiedene Industrien herzustellen, darunter Automobilbau, Luftfahrt, Maschinenbau und Werkzeugherstellung.
Wie funktioniert Gesenkschmieden?
Der Prozess besteht aus mehreren Schritten:
- Erwärmen des Werkstücks
- Das Rohmaterial (z. B. Stahl, Aluminium) wird auf eine hohe Temperatur erhitzt.
- Beim Warmgesenkschmieden sind das oft 1.100–1.300 °C für Stahl.
- Vorformen (optional)
- In manchen Fällen wird das Metall durch Walzen oder Vorpressen in eine grobe Form gebracht.
- Schmieden im Gesenk
- Das erhitzte Werkstück wird zwischen zwei Gesenken platziert.
- Eine Presse oder ein Hammer übt hohe Kräfte aus, wodurch das Metall in die gewünschte Form fließt.
- Grat entfernen
- Überschüssiges Material (der Grat) wird nach dem Schmieden entfernt.
- Wärmebehandlung (optional)
- Zur Verbesserung der Materialeigenschaften (z. B. Härte, Zähigkeit) kann eine Wärmebehandlung erfolgen.
- Endbearbeitung
- Falls nötig, wird das Bauteil durch Drehen, Fräsen oder Schleifen auf Maß gebracht.
Gesenkschmieden ist also ein unverzichtbares Verfahren für hochwertige Metallteile mit hoher Festigkeit und Präzision.
Unter „Schmieden“ wird generell das Freiformschmieden verstanden. Also das Schmieden ohne Gesenk/Werkzeugform. Diese Art zu schmieden ist gut für Einzelteile geeignet, die flexibel gefertigt werden sollen. Das Schmieden im Gesenk ermöglicht demgegenüber eine hohe Präzision und ist deshalb für die Serienfertigung sehr gut geeignet.
- Geschmiedet (Freiformschmieden)
- Formgebung durch gezielte Schläge oder Druck, ohne feste Form.
- Flexibel, aber weniger präzise.
- Ideal für Einzelstücke (z. B. große Wellen, Turbinenteile).
- Gesenkgeschmiedet (Gesenkschmieden)
- Metall wird in eine vorgefertigte Gesenkform gepresst.
- Hohe Präzision, ideal für Serienfertigung (z. B. Zahnräder, Pleuelstangen).
- Höhere Werkzeugkosten, aber wirtschaftlich bei großen Stückzahlen.
Für das Gesenkschmieden eignen sich vor allem Metalle mit guter Umformbarkeit bei hohen Temperaturen. Häufig verwendete Materialien sind:
- Stähle (am häufigsten genutzt)
- Kohlenstoffstähle (z. B. C45, C60) – hohe Festigkeit, gute Schmiedbarkeit
- Legierte Stähle (z. B. 42CrMo4, 34CrNiMo6) – für hochbelastete Bauteile
- Edelstähle (z. B. 1.4301, 1.4542) – korrosionsbeständig, aber schwerer zu schmieden
- Aluminiumlegierungen
- Leicht, korrosionsbeständig
- Genutzt in Luftfahrt, Automobilbau, Maschinenbau
- Beispiele: AlMgSi1, AlCu4Mg1
- Kupfer- und Messinglegierungen
- Gute elektrische Leitfähigkeit, Korrosionsbeständigkeit
- Genutzt für Armaturen, Elektrotechnik, Rohrverbindungen
- Beispiele: CuZn40, CuAl10Ni5Fe4
- Titanlegierungen
- Extrem leicht und fest, hitzebeständig
- Eingesetzt in Luftfahrt und Medizintechnik
- Beispiel: Ti6Al4V
- Nickelbasislegierungen
- Hohe Temperatur- und Korrosionsbeständigkeit
- Verwendung in Turbinen, Raumfahrt, Chemieindustrie
- Beispiel: Inconel 718
Zusammenfassung:
- Stähle → meistgenutzt, hohe Festigkeit
- Aluminium → leicht, für Luftfahrt/Autos
- Kupfer/Messing → gute Leitfähigkeit
- Titan/Nickel → für extreme Bedingungen
Welche Materialien bei Richter Formteile angeboten werden, erfahren Sie hier.
Das Gesenkschmieden wird in vielen Branchen eingesetzt, insbesondere dort, wo hochfeste, präzise geformte Metallbauteile erforderlich sind. Zu den wichtigsten Branchen gehören:
- Automobilindustrie
- Herstellung von Kurbelwellen, Pleuelstangen, Zahnrädern, Achsschenkeln und Lenkungskomponenten.
- Gesenkgeschmiedete Teile bieten hohe Festigkeit und Langlebigkeit, was in Fahrzeugen entscheidend ist.
- Luft- und Raumfahrt
- Produktion von Triebwerkskomponenten, Fahrwerksbauteilen und Strukturbauteilen.
- Leichte, aber extrem belastbare Bauteile sind hier essenziell.
- Eisenbahnindustrie
- Schmiedeteile für Radsätze, Achsen, Kupplungen und Fahrwerkskomponenten.
- Notwendig für hohe Belastungen und lange Lebensdauer.
- Maschinenbau & Anlagenbau
- Hochbelastbare Werkzeuge, Wellen, Zahnräder, Lager und Verbindungselemente.
- Notwendig für den Einsatz in schweren Maschinen.
- Öl- und Gasindustrie
- Hochdruckventile, Bohrwerkzeuge, Flansche und Pumpenbauteile.
- Schmiedeteile widerstehen extremen Temperaturen und Drücken.
- Land- und Baumaschinen
- Herstellung von Achsen, Zahnrädern, Schaufeln und anderen hochfesten Bauteilen.
- Erforderlich für robuste und langlebige Maschinen.
- Energiewirtschaft (Kraftwerke & Windkraftanlagen)
- Turbinenwellen, Generatorenbauteile, Flansche und Verbindungselemente.
- Hohe Beanspruchung durch mechanische und thermische Belastung.
- Medizintechnik
- Herstellung von chirurgischen Instrumenten und Prothesenkomponenten.
- Hochpräzise, korrosionsbeständige und biokompatible Werkstoffe sind gefragt.
Das Gesenkschmieden ist also in vielen Industriezweigen unersetzlich, da es Bauteile mit hoher Festigkeit, Präzision und Langlebigkeit liefert.
Das Gesenkschmieden bietet gegenüber anderen Schmiedeverfahren mehrere Vorteile, insbesondere in Bezug auf Präzision, Effizienz und Materialeigenschaften. Hier sind die wichtigsten Vorteile im Vergleich zu anderen Schmiedeverfahren:
- Homogenes Gefüge – hohe Belastbarkeit und Festigkeit.
- Hohe Maßgenauigkeit & Wiederholbarkeit – Präzise Formen reduzieren Nachbearbeitung.
- Höhere Festigkeit – Optimierter Faserverlauf verbessert die mechanischen Eigenschaften.
- Effiziente Serienfertigung – Schneller und kostengünstiger als Freiformschmieden.
- Geringer Materialverlust – Weniger Verschnitt als bei anderen Verfahren.
- Komplexe Geometrien möglich – Ideal für Automobil-, Luftfahrt- und Maschinenbau.
- Gute Oberflächenqualität – Reduziert den Bedarf an Nachbearbeitung.
Das Gesenkschmieden ist besonders vorteilhaft für Serienproduktion, komplexe Bauteile und hohe mechanische Belastbarkeit. Im Vergleich zum Freiformschmieden bietet es höhere Präzision, weniger Nachbearbeitung und effizientere Materialnutzung, während es gegenüber dem Walzenschmieden flexibler für verschiedene Geometrien ist.
Die Präzision beim Gesenkschmieden ist sehr hoch und hängt von mehreren Faktoren wie der Qualität des Gesenks, der Presskraft und dem Werkstoff ab. Typische Maßtoleranzen liegen im Bereich von ±0,3 mm bis ±1 mm, abhängig von der Bauteilgröße und der Nachbearbeitung.
Faktoren, die die Präzision beeinflussen:
- Gesenkkonstruktion – Hochwertige Gesenke sorgen für exakte Formgebung.
- Materialverhalten – Unterschiedliche Metalle reagieren unterschiedlich auf den Schmiedeprozess.
- Presskraft & Temperatur – Optimale Parameter minimieren Maßabweichungen.
- Nachbearbeitung – Schmiedeteile werden oft durch Fräsen oder Schleifen verfeinert.
Gesenkschmieden bietet hohe Präzision, besonders für Serienfertigung und kann durch Nachbearbeitung weiter verbessert werden.
Trotz vieler Vorteile hat das Gesenkschmieden auch einige Einschränkungen und Nachteile:
- Hohe Werkzeugkosten – Lohnt sich nur für große Serien.
- Begrenzte Geometrien – Sehr komplexe oder große Teile schwer umsetzbar.
- Materialverlust – Gratbildung erfordert Nachbearbeitung.
- Hoher Energiebedarf – Schmiedepressen verbrauchen viel Energie.
- Werkstoffbegrenzung – Nicht alle Materialien sind gut schmiedbar.
Gesenkschmieden ist ideal für serienmäßige, hochbelastbare Bauteile, aber hohe Werkzeugkosten und geometrische Einschränkungen machen es weniger geeignet für Kleinserien oder Sonderanfertigungen.