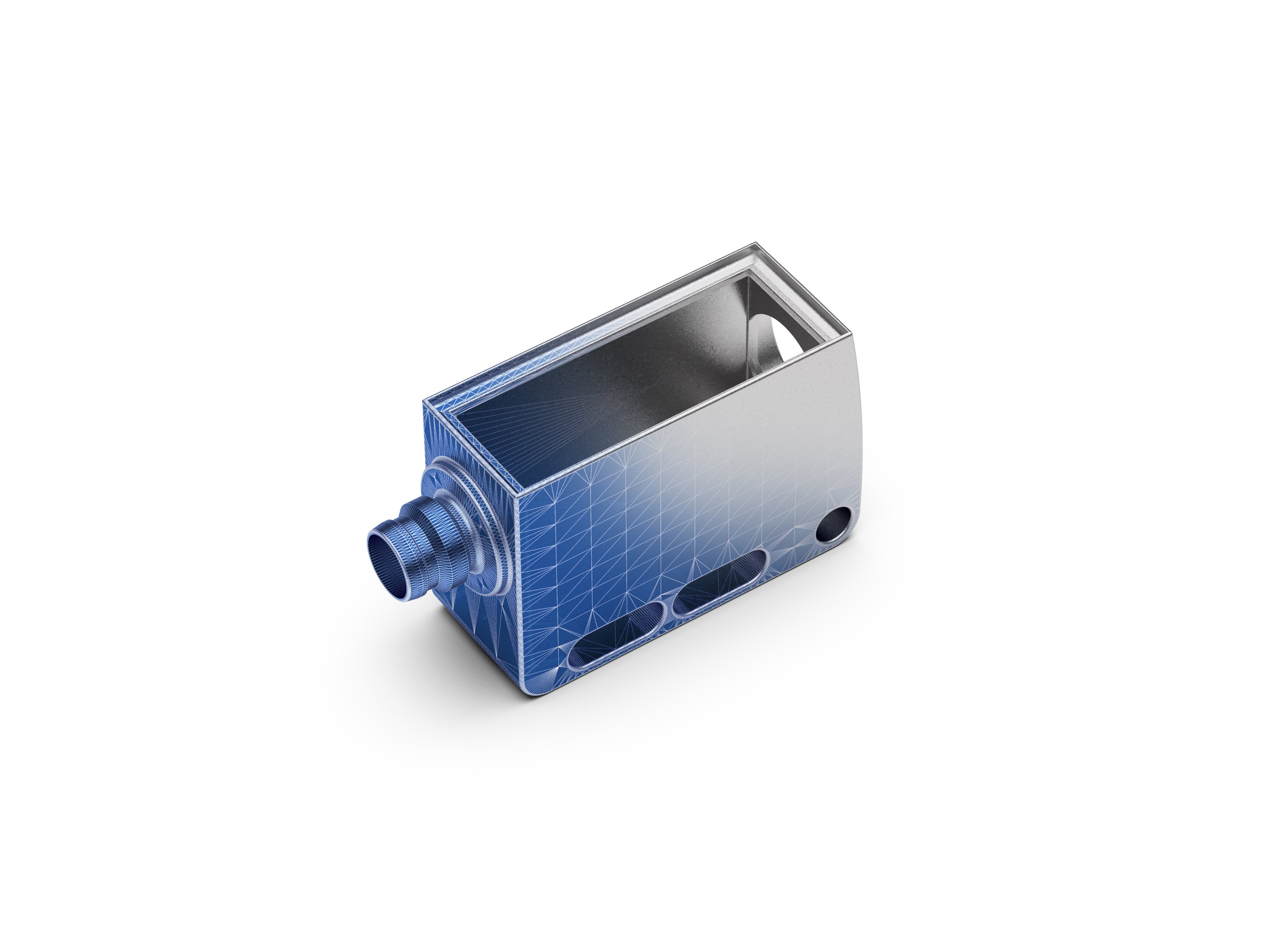
MIM-Verfahren
1. Definition
Die MIM Technologie, auch Metallpulverspritzguss (eng. Metal Injection Moulding) genannt, kombiniert zwei Technologien: das Spritzgießen (aus dem Kunststoffspritzguss bekannt) und die Sinter-Technologie.
Aufgrund der Umsetzung von hohen geometrisch komplexen Anforderungen bereits im Produktionsprozess, wird diese Technologie als konturnahes Herstellungsverfahren bezeichnet.
Bei diesem Urformverfahren werden feines Metallpulver und thermoplastisches Polymerharz vermischt um ein spritzfähiges Granulat, den Feedstock, zu erhalten. Der so gewonnene Grünling wird nach dem Abkühlen entbindert um den Kunststoff herauszulösen. Der entstandene Bräunling hat noch eine poröse Oberfläche und wird deshalb knapp unter der Schmelztemperatur gesintert.
Der Vorteil des MIM Verfahren ist die vielfältige Auswahl an Formgebungsmöglichkeiten und Werkstoffen. Besonders geeignet ist die MIM Technik bei der Herstellung von kleineren und mittelgroßen Metallteilen von komplexer Geometrie in mittleren und großen Serien.
Während bei anderen Verfahren mehrere Bauteile separat produziert und zu einer Bauteilgruppe montiert werden müssen, kann im MIM Prozess gleich ein Bauteil aus einem Stück hergestellt werden. Auch Bohrungen, Gewinde, Hinterschneidungen, Gravuren, u.v.m. können in einem Produktionsschritt hergestellt werden.
2. Ablauf des MIM Verfahrens
1. Mischen
2. Feedstock
3. Spritzgießen
4. Entbindern
5. Sintern
6. Endkontrolle
3. Video: Prozessablauf beim MIM Verfahren
4. Ursprung des Metallpulverspritzguss
Die MIM Technik ist bereits seit fast einem Jahrhundert bekannt: Erste keramische Gehäuse für Zündkerzen wurden schon 1920 mit Metallpulverspritzguss hergestellt.
Richtig in der Industrie angekommen ist das MIM Verfahren dann aber erst 1980. Zunächst wurden mit MIM kleine, hochpräzise metallische Formteile für Industriegüter produziert.
Mittlerweile ist die MIM Technik aus der Industrie nicht mehr wegzudenken. Das MIM Verfahren hat sich als hochwirtschaftliches Fertigungsverfahren für Großserienprodukte etabliert, das besonders bei hoher Komplexität zum Einsatz kommt.
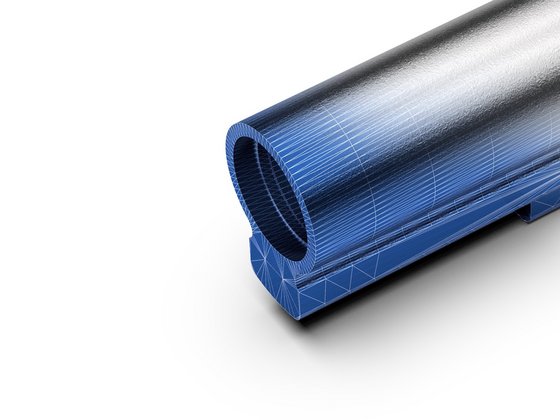
Sie benötigen MIM-Bauteile?
Informieren Sie sich hier über die Spezifika des MIM-Verfahrens bei Richter Formteile.
Service - ganz nach Ihrem Bedarf
Wir verstehen uns als Ihr Partner über die Wertschöpfungskette hinweg.
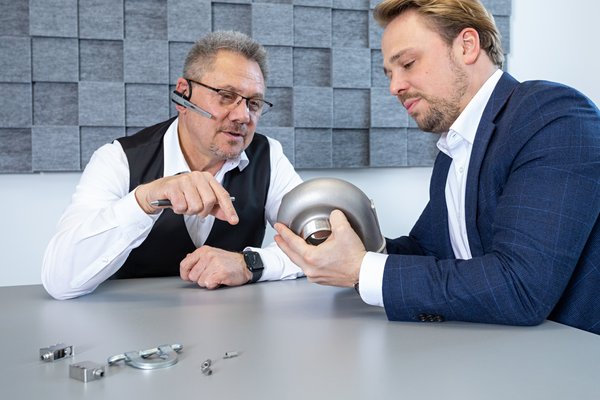
Technische Beratung
Gerne unterstützen wir Sie bei fachlichen Fragen ✓ Stimmen Sie Ihre Anforderungen und die technische Zeichnungen mit unserem Fachpersonal ab!
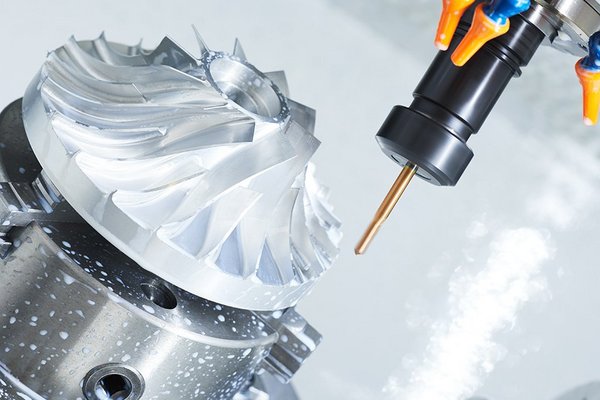
Bearbeitung / Baugruppen
Umfassende Bearbeitung, Oberflächenbehandlung von Formteilen ✓ Vormontage und Montage von Baugruppen ✓ Teilen Sie uns jetzt Ihre Anforderungen mit!
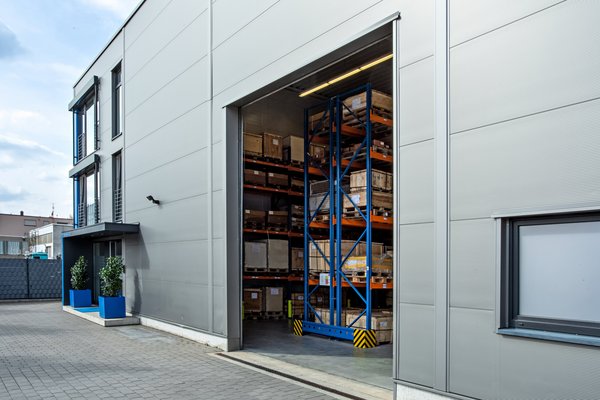
Supply Chain Management
Wir kümmern uns neben der Entwicklung und Produktion der Bauteile auch um ✓ Beschaffung ✓ Logistik ✓ Verzollung - Jetzt informieren und Vorteile nutzen!
In allen Branchen zu Hause
Wir sind in der Branche zuhause, wo unsere Kunden sind. Erfahren Sie hier mehr zu unseren Referenzen.
Antriebstechnik
Armaturen und Pumpen
Bauindustrie
Elektroindustrie
Fahrzeugbau
Filtertechnik
Land- und Forstwirtschaft
Lebensmittelindustrie
Maschinenbau
Medizintechnik
5. Fragen und Antworten rund um das MIM-Fertigungsverfahren
FAQs zum MIM-Verfahren
MIM steht für Metal Injection Molding (deutsch: Metallspritzguss). Es ist ein Fertigungsverfahren, das die Vorteile der Kunststoff-Spritzgusstechnik mit der Metallverarbeitung kombiniert.
MIM ermöglicht die Herstellung komplexer, präziser Metallteile durch das Einspritzen eines Metallpulver-Kunststoff-Gemischs in eine Form. Nach dem Spritzgießen wird das Bindemittel entfernt und das Bauteil gesintert, wodurch es seine endgültige Festigkeit erhält.
MIM eignet sich besonders für kleine, hochpräzise Metallteile in der Medizintechnik, Automobilindustrie, Luftfahrt und Elektronik.
Das Metallpulverspritzgussverfahren (MIM – Metal Injection Molding) eignet sich besonders für komplexe, kleinformatige Metallteile mit hoher Präzision. Typische Anwendungsbereiche und klassische Bauteile, die mit dem MIM-Verfahren produziert werden, sind:
- Automobilindustrie
- Zahnräder & Getrieberäder
- Ventilteile
- Einspritzsystemkomponenten
- Sensor- und Aktuatorgehäuse
- Schalt- und Kupplungskomponenten
- Medizintechnik
- Chirurgische Instrumente (z. B. Zangen, Scheren)
- Minimalinvasive OP-Werkzeuge
- Zahnimplantatkomponenten
- Endoskopische Bauteile
- Uhren- und Schmuckindustrie
- Hochpräzise Uhrwerke & Zahnräder
- Verschlüsse für Armbänder
- Dekorative Metallteile mit komplexen Designs
- Luft- und Raumfahrt
- Kleinbauteile für Triebwerke
- Strukturkomponenten mit hoher Temperaturbeständigkeit
- Sensorengehäuse
- Elektronik & Telekommunikation
- Smartphone- & Laptopgehäuse
- Steckverbinder & Kontaktstifte
- Kühlkörper
- Waffen- und Sicherheitsindustrie
- Abzugsmechanismen
- Verschlusssysteme
- Sicherungselemente
MIM eignet sich vor allem für Bauteile, die eine hohe Festigkeit, komplizierte Geometrien und feine Strukturen erfordern. Besonders vorteilhaft ist es bei hohen Stückzahlen, da es kosteneffizienter als spanende Fertigungsverfahren ist.
Das MIM-Verfahren (Metal Injection Molding) bietet zahlreiche Vorteile:
- Hohe Designfreiheit – Komplexe Geometrien, dünne Wände, Funktionsintegration.
- Exzellente Materialeigenschaften – Hohe Festigkeit, Dichte (95–98 %), Materialvielfalt (Edelstahl, Titan, Wolfram etc.).
- Hohe Präzision – Enge Toleranzen (ca. +/- 0,3 % vom Nennmaß), kaum Nachbearbeitung nötig.
- Effiziente Massenproduktion – Kostensparend, geringer Materialverlust, ideal für hohe Stückzahlen.
- Hochwertige Oberflächen – Feine Strukturen, geringe Rauheit (Ra 3,2 µm).
- Nachhaltigkeit – Materialrecycling & energieeffiziente Fertigung.
- Perfekt für kleine & filigrane Bauteile – Ideal für Medizintechnik, Automobilbau & Elektronik.
MIM kombiniert die Designfreiheit des Spritzgusses mit der Festigkeit von Metall – ideal für präzise, komplexe Bauteile in Serie.
Das MIM-Verfahren (Metal Injection Molding) unterscheidet sich in mehreren Aspekten von CNC-Bearbeitung und Gießen. Hier die wichtigsten Unterschiede:
- Geometrische Komplexität
- MIM: Ermöglicht hochkomplexe Formen, Hinterschneidungen und dünnwandige Strukturen ohne zusätzliche Bearbeitung.
- CNC: Begrenzte Designfreiheit, komplexe Formen erfordern zusätzliche Bearbeitungsschritte.
- Gießen: Gute Formvielfalt, aber nicht so präzise wie MIM und oft mit Nachbearbeitung verbunden.
- Präzision & Toleranzen
- MIM: Hohe Maßhaltigkeit, oft keine Nachbearbeitung nötig.
- CNC: Extrem hohe Präzision (bis in den Mikrometerbereich), ideal für Einzelteile und Kleinserien.
- Gießen: Geringere Maßhaltigkeit, oft Nachbearbeitung erforderlich.
- Materialauswahl & Eigenschaften
- MIM: Hohe Dichte, sehr gute mechanische Eigenschaften vergleichbar mit gewalztem oder geschmiedetem Metall.
- CNC: Verwendet massive Metallblöcke, daher beste Materialeigenschaften, aber hoher Materialverlust.
- Gießen: Kann spröder sein (Poren, Lunkerbildung), mechanische Eigenschaften oft schlechter als MIM.
- Wirtschaftlichkeit & Serienfertigung
- MIM: Besonders wirtschaftlich für hohe Stückzahlen (Serienproduktion).
- CNC: Hohe Kosten für große Stückzahlen, aber ideal für Einzelteile und Prototypen.
- Gießen: Geeignet für große Bauteile und hohe Stückzahlen, aber oft mit Nachbearbeitungskosten verbunden.
- Nachhaltigkeit & Materialeffizienz
- MIM: Sehr geringer Materialverlust, da Metallpulver wiederverwendet werden kann.
- CNC: Hoher Materialverlust durch Spanabtragung.
- Gießen: Materialausnutzung besser als CNC, aber nicht so effizient wie MIM.
Fazit:
- MIM eignet sich für kleine, komplexe Bauteile in großen Stückzahlen.
- CNC-Bearbeitung ist ideal für hochpräzise Einzelteile & Kleinserien.
- Gießen ist vorteilhaft für große, weniger komplexe Bauteile.
Das Metallpulverspritzgussverfahren (MIM – Metal Injection Molding) wird in vielen Branchen eingesetzt, insbesondere dort, wo komplexe, präzise und hochfeste Metallbauteile in großen Stückzahlen benötigt werden.
- Automobilindustrie
- Zahnräder, Getrieberäder, Kupplungsteile
- Einspritzsysteme, Sensor- & Aktuatorgehäuse
- Schlossmechanismen, elektrische Kontakte
- Medizintechnik
- Chirurgische Instrumente (Zangen, Scheren)
- Minimalinvasive OP-Werkzeuge
- Zahnimplantate & kieferorthopädische Bauteile
- Luft- & Raumfahrt
- Kleinbauteile für Triebwerke & Turbinen
- Strukturkomponenten mit hoher Temperaturbeständigkeit
- Sensor- & Aktorgehäuse
- Uhren- & Schmuckindustrie
- Präzise Uhrwerke, Zahnräder, Federn
- Hochwertige Gehäuse & Armbandverschlüsse
- Dekorative Metallelemente
- Elektronik & Telekommunikation
- Steckverbinder, elektrische Kontakte
- Kühlkörper für Mikrochips
- Smartphone- & Laptopgehäuse
- Waffen- & Sicherheitsindustrie
- Abzugsmechanismen, Sicherungselemente
- Gehäuse für optische & elektronische Zielsysteme
- Industrielle Anwendungen
- Schneidwerkzeuge, Messer & Klingen
- Pumpenteile, Ventile, Lager
- Hochpräzise mechanische Komponenten
MIM ist besonders attraktiv für Branchen, die kleine, komplexe und hochbelastbare Metallteile in hoher Stückzahl und hoher Präzision benötigen.