Verzinken: das Verzinkungsverfahren
Inhaltsverzeichnis
1. Definition: Was ist Verzinken?
Das Verzinken ist ein Beschichtungsverfahren, bei dem Halbzeuge, Bauteile oder Baugruppen aus Eisen oder Stahl mit einer dünnen Schicht aus reinem Zink überzogen werden. Dies kann mit unterschiedlichen Verfahren geschehen. Im Vergleich mit anderen Beschichtungsarten bewirkt das Verzinken zusätzlich zur passiven Beschichtung einen aktiven Korrosionsschutz. Dies bedeutet, dass die Zinkschicht gegenüber dem Eisen eine kathodische Wirkung hat und als Opferanode wirkt. Dies erhöht die Lebensdauer der beschichteten Teile deutlich.
2. Verschiedene Verzinkungsarten: Welche Verfahren gibt es?
Um ein Bauteil mit einer Zinkschicht zu versehen, existieren eine Reihe unterschiedlicher Methoden. Die in der Praxis am häufigsten Angewendeten sind:
- Feuerverzinken (Schmelztauchverzinken)
- galvanisches Verzinken (Elektrolytverzinken)
- mechanische Verzinkung
- Spritzverzinken
- Sherardisieren (Diffusionsverzinken)
Aufgrund der teils beträchtlichen Verfahrensunterschiede ist der Begriff „Verzinken“ nur mit Einschränkungen aussagefähig. Laut technischem Sprachgebrauch ist das übereinstimmende Element aller Verzinkungsverfahren das Erzeugen eines korrosionsabweisenden Überzuges aus reinem Zink. Beschichtungsarten, die mit Zinkstaubfarben funktionieren oder das Zinklamellenbeschichten gehören demnach nicht zum Verzinken.
3. Die Feuerverzinkung
3.1 Was ist Feuerverzinken und wie funktioniert es?
Beim Feuerverzinken wird der Zinküberzug durch das Eintauchen des vorbehandelten Werkstücks oder Bauteils in eine flüssige Zinkschmelze erzeugt. Die Temperatur des Zinkbades beträgt rund 450 °C. Zusätzlich unterscheidet der Techniker zwischen dem Stückverzinken und dem kontinuierlichen Feuerverzinken, häufig auch Sendzimir-Verzinken, Endlosverzinken oder Bandverzinken genannt.
Ein typisches Anwendungsgebiet für das Stückverzinken ist die Beschichtung eines individuell hergestellten Treppengeländers, um es dauerhaft vor Rost zu schützen. Halbzeuge wie Bleche, Bänder oder Profile werden zumeist kontinuierlich verzinkt. In beiden Verfahren werden unterschiedliche Zink-Schichtdicken erzielt. Während die Zinkschicht beim Stückverzinken zwischen 50 und 150 Mikrometer beträgt, werden beim kontinuierlichen Feuerverzinken lediglich Schichtdicken bis 40 Mikrometer erreicht.
3.2 Merkmale der Stück- und Bandverzinkung auf einen Blick:
Stückverzinkung
- ideal für einzelne, individuell gefertigte Bauteile und Konstruktionen
- Eintauchen des vorbehandelten Werkstückes insgesamt in die flüssige Zinkschmelze
- hohe Schichtdicken erreichbar
- robuster, langlebiger Korrosionsschutz
- Bauteile sind rundum, innen und außen, auch an den Schnittkanten zuverlässig vor Korrosion geschützt
Kontinuierliches Verzinken (Bandverzinkung)
- Vorprodukte wie Stahlbänder oder Profile laufen vor der Weiterverarbeitung kontinuierlich durch ein Zinkbad.
- geringere Zink-Schichtdicke als bei der Stückverzinkung
- durch nachfolgendes Stanzen, Zuschneiden etc. wird die Zinkschicht an den Schnittkanten zerstört
3.3 Worin bestehen die Vor- und Nachteile der Feuerverzinkung?
Vorteile des Feuerverzinkens
Neben dem robusten Langzeitkorrosionsschutz bietet das Verfahren eine Reihe weiterer Vorteile:
- umweltfreundliches Verfahren mit hoher Wirtschaftlichkeit.
- hohe Schlag-, Stoß- und Kratzfestigkeit.
- kathodischer Rundum-Korrosionsschutz, auch an den Kanten, an schwer zugänglichen Stellen und in Hohlräumen
- wartungsfrei
- funktionell ansprechende Optik
Nachteile des Feuerverzinkens
- Gefahr des Bauteilverzugs aufgrund hoher Zinkbadtemperatur
- Oberfläche leicht rau, keine dekorative Oberflächengestaltung möglich
- u.U. Nacharbeit von Gewinden, Abtropfnasen und scharfen Abtropfkanten erforderlich
- Limitation infolge der Größe der Bauteilkonstruktion oder bei Lochblechen aufgrund der Lochgröße
3.4 Welche Normen gelten für die Feuerverzinkung?
Das wichtigste Regelwerk für das Stückverzinken ist die DIN EN ISO 1461. Diese Norm ist europaweit gültig. Als ISO-Norm ist sie darüber hinaus auch weltweit von Bedeutung. In der Norm sind sämtliche Anforderungen an das Feuerverzinken von Einzelteilen sowie die entsprechenden Prüfvorschriften festgeschrieben. Allerdings definiert die DIN EN ISO 1461 lediglich die Leistungen, die der Verzinkungsfachbetrieb erbringen muss. Für Fehlstellen, die beim nachfolgenden Transport oder bei der Montage der verzinkten Teile entstehen, ist die Feuerverzinkerei nicht zuständig. Für das kontinuierliche Bandverzinken kommen die DIN EN 10346 und die DIN EN 10143 zur Anwendung. In diesen Normen sind sämtliche Anforderungen und Prüfvorschriften bezüglich Beschaffenheit und Dicke des Zinküberzuges festgelegt. Auch das qualifizierte Ausbessern von Fehlstellen wird ausführlich erklärt. Das Verzinken von Stacheldraht unterliegt mit der DIN EN ISO 10244-1 und -2 einer eigenen Norm.
4. Die galvanische Verzinkung
In der Galvanik ist das Verzinken ein Verfahren, welches einerseits dem Korrosionsschutz und andererseits der Oberflächenveredelung verschiedenster Stahlteile dient. Da sie vergleichsweise wirtschaftlich ist, kommt die galvanische Verzinkung beispielsweise in der Automobilindustrie sehr häufig zum Einsatz. Bei dem Verzinkungsverfahren entsteht der Zinküberzug mithilfe eines elektrischen Stroms. Dafür werden die zu verzinkenden Bauteile in ein saures oder in ein alkalisches Elektrolytbad eingetaucht, wo sie als Kathode wirken. Die als Anode wirkende Elektrode besteht aus reinem Zink. Während der Verzinkung geht der Stahl mit dem Zink keine Legierung ein. Es bildet sich eine vergleichsweise dünne Zinkschicht, welche die galvanisch verzinkten Teile hervorragend vor Korrosion schützt.
4.1 Worin bestehen die Vor- und Nachteile des galvanischen Verzinkens?
Vorteile der galvanischen Verzinkung
- hohe Konturgenauigkeit
- keine Tropfenbildung
- Gewinde bleiben gängig, Passungen bleiben gewährleistet
- kein Bauteilverzug infolge niedriger Verzinkungstemperaturen (max. 70 °C)
- wirtschaftliches Korrosionsschutz- und Beschichtungsverfahren
- moderne Optik
Nachteile der galvanischen Verzinkung
- der Zinküberzug ist bedeutend dünner (Schichtdicke circa 5 bis 7 Mikrometer) als beim Feuerverzinken
- der Korrosionsschutz ist kurzlebiger als bei anderen Verzinkungsarten
- bei gehärteten Teilen besteht die Gefahr einer Wasserstoffversprödung
5. Die mechanische Verzinkung
Beim mechanischen Verzinken, von Experten häufig auch „mechanical plating“ genannt, wird die gegen Korrosion schützende Zinkbeschichtung ohne thermische oder elektrolytische Einwirkung geschaffen. Damit ist diese Verzinkungsart für verzugsgefährdete sowie für gehärtete Teile wie Schrauben, Muttern oder Kleinteile aus Federstahl ideal. Der Verzinkungsprozess läuft vollautomatisch in einer rotierenden Trommel ab, die mit einer chemischen Substanz, Glaspulver und Zinkpulver gefüllt ist. Während die Glasperlen das Zinkpulver quasi auf das Bauteil „aufhämmern“ stellt eine kontrollierte chemische Reaktion sicher, dass zwischen dem Stahl und dem Zink eine feste Bindung entsteht. Mit dem mechanischen Verzinken werden sehr gleichmäßige Zinkoberflächen erzielt. Allerdings sind die dekorative Optik und die Haftbeständigkeit deutlich schlechter als beim galvanischen Verzinken, sodass die mechanische Verzinkung in der Praxis vergleichsweise selten zum Einsatz kommt und ihre Anwendung stets sorgfältig abgewogen wird.
6. Die Spritzverzinkung
Beim Spritzverzinken wird ein Draht aus reinem Zink mithilfe einer Flamme oder eines Lichtbogens angeschmolzen, durch Druckluft in kleinste Partikel zerstäubt und gezielt auf das Werkstück aufgespritzt. Wichtig ist, dass die Bauteile, Werkstücke oder Konstruktionen vor dem Verzinken gesandstrahlt wurden. Durch das Sandstrahlen bildet sich eine poröse Oberfläche aus, an der die Zinkpartikel sehr gut haften, sodass eine feste, langlebige Korrosionsschutzschicht entsteht. Wie beim mechanischen Verzinken ist auch beim Spritzverzinken die thermische Belastung vernachlässigbar gering. Damit eignet sich das Verfahren sehr gut für verzugsgefährdete Konstruktionen und große Flächen. Bei schwer zugänglichen Stellen, Hinterschneidungen und Hohlräumen gerät das Spritzverzinken jedoch an seine Grenzen, sodass es sich für Behälter, Innenrohre und ähnliche Bauteile nicht eignet.
7. FAQ: Häufige Fragen rund um das Verzinken
Verzinken
Der Korrosionsschutz wird prinzipiell durch folgende zwei Prinzipien erreicht:
- Passiver Korrosionsschutz: Die Zinkschicht schirmt den Stahl von der korrosiven Umgebung ab, wobei die Zinkoberfläche selbst eine natürliche Patina ausbildet, welche die Zinkkorrosion extrem verlangsamt.
- Aktiver Korrosionsschutz: In einer korrosionsfördernden Umgebung bilden der Werkstoff Eisen und das aufgebrachte Zink ein sogenanntes „Lokalelement“. Dies bedeutet, dass sich das unedlere Zink für das edlere Eisen „opfert“, indem es Elektronen abgibt. Das Zink löst sich also geringfügig auf, während der Stahl erhalten bleibt.
Diese Frage lässt sich nicht pauschal beantworten. Das gewählte Verfahren hängt immer von Art der Bauteile, der Bauteilgeometrie und den Anforderungen an den Korrosionsschutz sowie der gewünschten Oberfläche ab. Vorteile der beiden Verzinkungsverfahren wie beispielsweise die bessere mechanische Beanspruchbarkeit oder längere Lebensdauer von feuerverzinkten Teilen müssen gegen Nachteile wie möglicher Verzug, zugelaufene Bohrungen oder gröbere Oberflächenstruktur abgewogen werden (siehe Vor- und Nachteile der verschiedenen Verzinkungsarten).
Für manche technische Anwendungen reicht die Dicke des Zinküberzuges nicht aus, um das Werkstück zuverlässig vor Korrosion zu schützen. Eine Steigerung der Schutzwirkung ist dann durch eine zusätzliche Farbbeschichtung, beispielsweise durch Nassbeschichtung oder Pulverbeschichtung, möglich. Durch die ergänzende Farbschicht wird die Zinkoberfläche vor chemischen Angriffen oder vor Umwelteinflüssen geschützt, sodass sich deren Lebensdauer deutlich erhöht. Die Schutzdauer für verschiedene Duplex-Beschichtungssysteme ist in der DIN EN ISO 12944-1 definiert.
Der Zinküberzug soll runter? Zum Entzinken (Entfernen von Zink) eigenen sich Salzsäure, Natron- oder Kalilauge, wobei das Werkstück einige Tage in der Lösung verbleiben muss. Je nach Legierung besteht die Gefahr, dass mit dem Abtragen der Zinkschicht auch das darunter liegende Metall angegriffen wird. Deshalb sollte das Entzinken von einem erfahrenen Profi oder in einer Verzinkerei vorgenommen werden.
Fehlstellen, die mit dem Verzinken im direkten Zusammenhang stehen, muss die Verzinkerei fachgerecht ausbessern. Sollten während des Transports oder der Montage verzinkter Teile Beschädigungen auftreten, ist folgendermaßen vorzugehen:
Entfernen etwaiger Verunreinigungen
- Vorbereitung der Oberfläche, etwa durch Schleifen oder chemische Behandlung
- Auswahl eines geeigneten Ausbesserungsstoffes, z. B. Zink-Anstrich aus der Dose
- sorgfältiges Auftragen unter Beachtung der erforderlichen Schichtdicke und der Überlappung mit dem unversehrten Zinküberzug
Für Außengewinde gibt es spezielle Klebebänder, die vor dem Eintauchen in das Zinkbad aufzubringen sind. Innengewinde lassen sich durch eine hitzebeständige Farbe oder das Eindrehen einer passenden Schraube schützen.
Suchen Sie weitere Möglichkeiten der Bearbeitung?
Ihre über uns produzierten Metall-Bauteile liefern wir als Rohteile oder bearbeitet, veredelt oder als Baugruppe montiert.
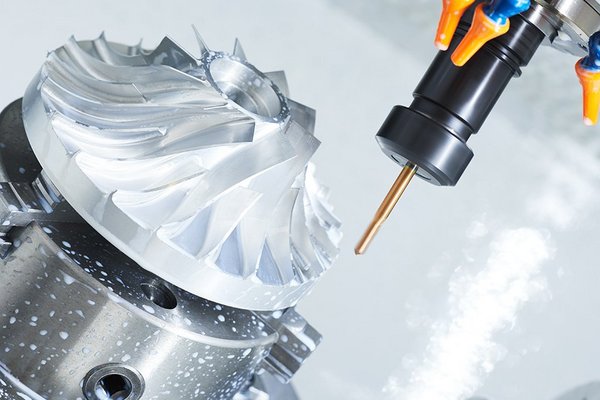
Bearbeitung / Baugruppen
Umfassende Bearbeitung, Oberflächenbehandlung von Formteilen ✓ Vormontage und Montage von Baugruppen ✓ Teilen Sie uns jetzt Ihre Anforderungen mit!
Weitere Fachbegriffe im Glossar:
- Baugruppen
- Bräunling (MIM Verfahren)
- Dampf-Autoklav
- DIN ISO
- Elektropolieren
- Eloxieren / Eloxal-Verfahren
- Entbinderung (MIM-Verfahren)
- Feedstock (Granulat)
- Formschlicker (Feingussverfahren)
- Gesenk
- Grünling (MIM-Verfahren)
- ISO 14001:2015
- ISO 9001:2015
- Kerbschlagzähigkeit
- KTL-Beschichtung
- Legierung in der Metallurgie
- Magnetpulverprüfung / Fluxen
- Materialverlust
- Metallische Werkstoffe
- Passivieren
- Prototyp
- Pulverbeschichtung
- Reproduzierbarkeit
- Rohling (Werkstück)
- Strahlen
- Verzinken: das Verzinkungsverfahren
- Vorfinanzierung
- Wachsbaum (Feingussverfahren)
- Wachsmodell (Feingussverfahren)
- Wachsspritzwerkzeug (Feingussverfahren)
- Zugfestigkeit
- Zunderschicht