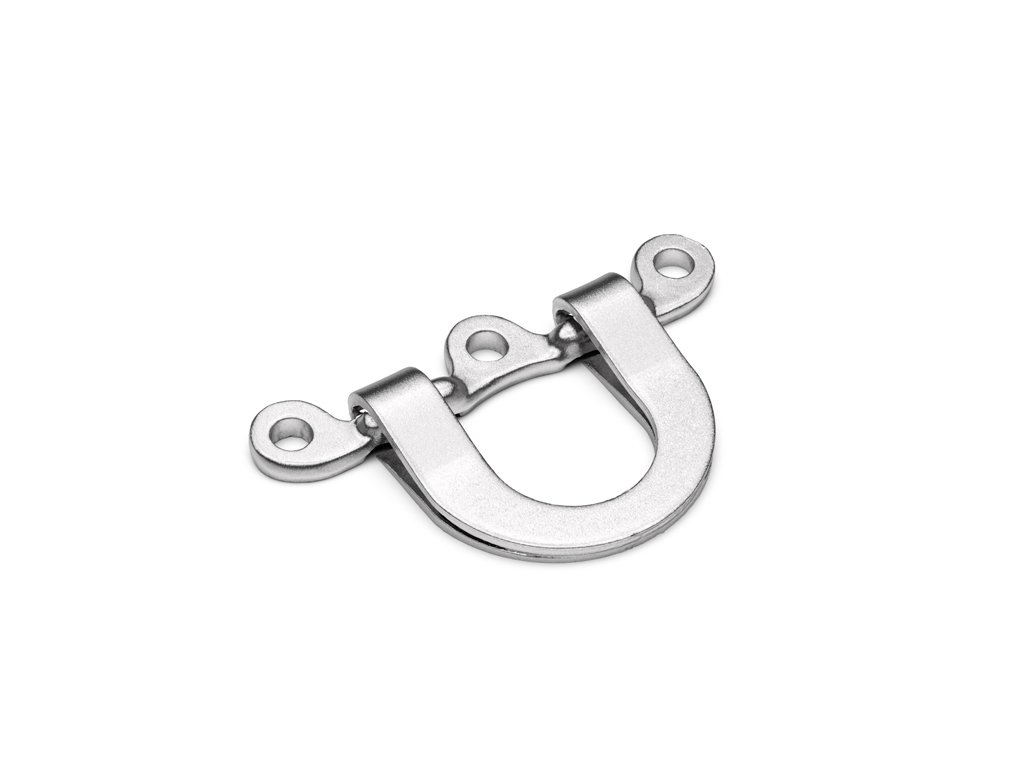
Drop Forging
Durable and pore-free components by drop forging
Drop forging creates forgings with an optimal fiber alignment and first-class strength. The forgings convince through a homogeneous, dense structure, which has neither pores nor other cavities. Forgings are reproducible with only one tool in large numbers at constant precision.
With over 40 years of experience in drop forging, we have excellent expertise in this field and are the ideal manufacturer for you. According to your ideas and goals, we determine the process, alloy and the properties of the component in a joint consultation.
Non-binding offer!

Advantages of drop forging
- ideal for complex shapes
- high reproducibility
- longevity
- homogeneous structure
- short processing time
The drop forging process at Richter Formteile
Below we provide information on the most important key data of the drop forging process in our company: specifications, materials as well as testing options and possible surface treatments.
standard weight:
0.04 - 150 kg
production:
Europe, Asia
certified acc. to:
DIN ISO 9001, 14001, TS 16949
materials:
steel, stainless steel alloys and aluminum
post-processing:
own CNC processing centers, heat treatments according to customer specifications
approvals in the fittings area:
AD 2000 and TRD 100
Die forged materials
In general, all kneadable metals can be used after they have been heated. These include steel, magnesium, aluminum, stainless steel as well as brass, copper and their alloys.
Machining, surface processing and testing options
Take advantage of our extensive service package and put together services according to your needs.
Testing options for forged pieces
- 3D laser or measuring probe
- chemical analysis
- fluxing
- impact strength
- tensile strengths
- ultrasound
- x-Ray
- yield point
- according to customer requirements
Surface treatments of forged parts
- anodizing
- CED coating
- electropolishing
- galvanizing (chrome-6 free)
- glass or sand bead blasting
- paint
- passivation
- powder coating
- prime
- radiation
- vibratory finishing
- according to customer requirements
We will gladly advise you!
Do you have further questions about investment casting in our company? Contact my team or me at any time. Your projects are our challenge! Or use our forms to place your request, message or confidentiality agreement.
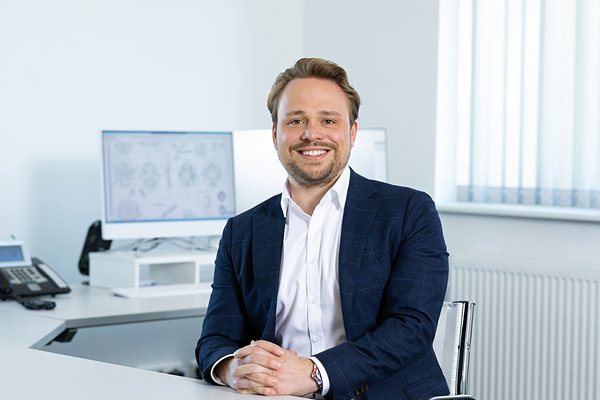
Timo Richter
Managing Director
Our strengths - your advantages
expert advice
in each casting and forging process
no risk
through conformity with drawings and ISO-certifications
optimal resource planning
through our international production network
secure processing
as a German legal partner
just in time delivery
ex warehouse Leonberg nearby Stuttgart in Germany
high process competence
through over 40 years of experience
maximum economy
through optimal resource planning
pre-financing
and storage of the complete annual requirement
Service – to suit your needs
All about Drop Forging
How does bulk forming work? What is the background of the forging process? We would be happy to give you a comprehensive overview.
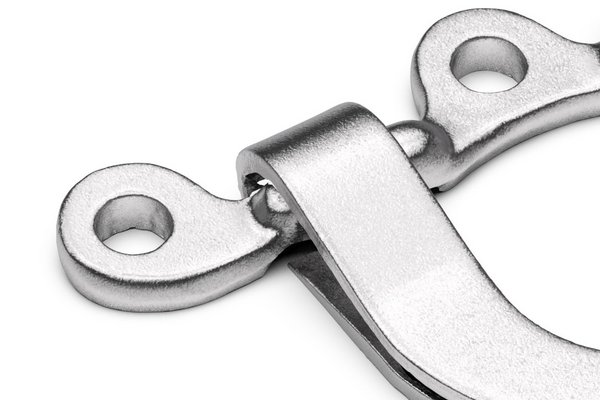
Drop Forging Procedure
Drop forging process: Optimal fibre flow with first-class structural strength. We explain the exact process in detail (with video).