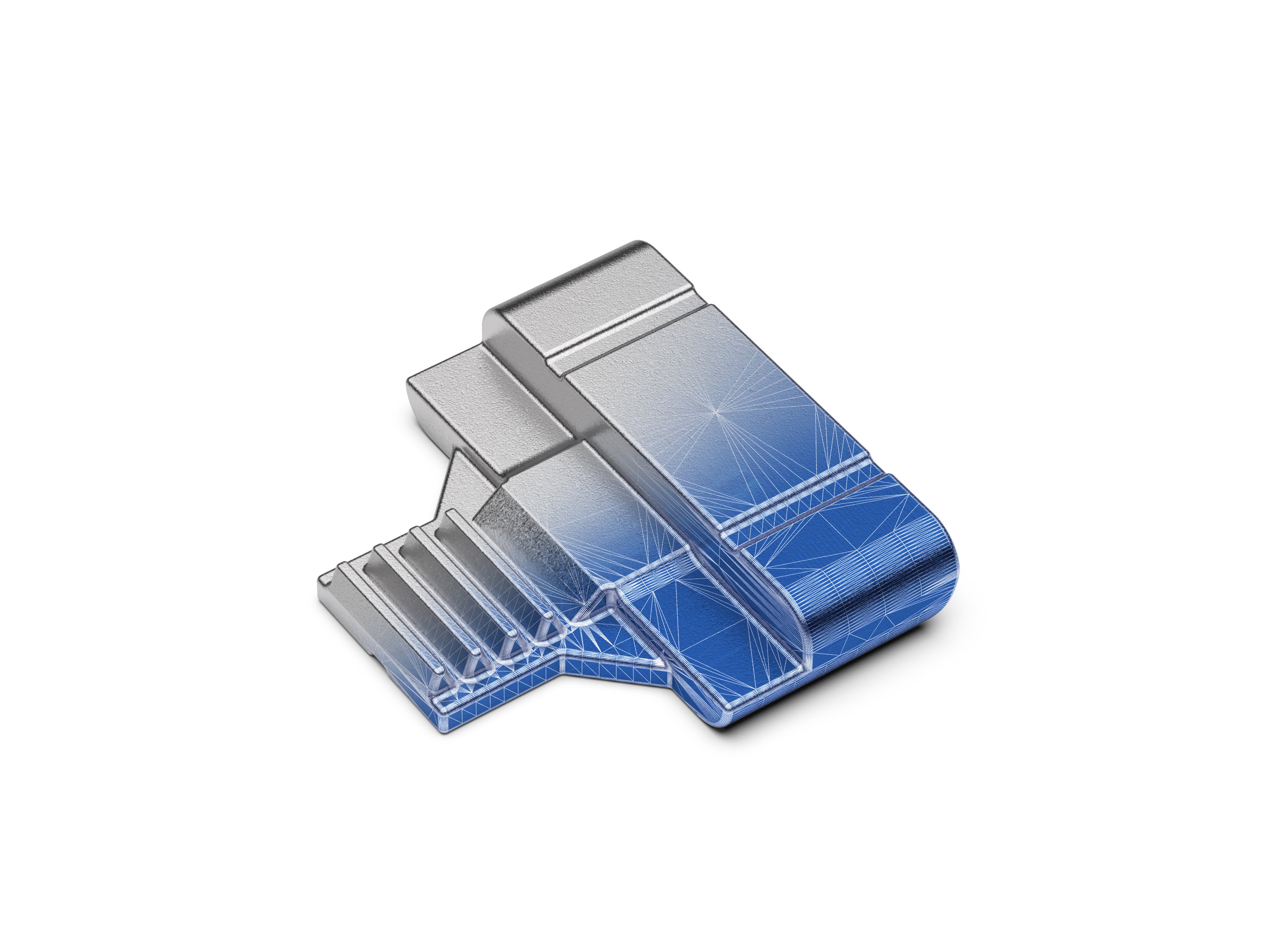
Investment casting procedure / lost-wax casting procedure
1. Definition
The lost wax process is the production of high-precision castings from metallic materials in a foundry. The original form of the process is characterized by high dimensional accuracy, first-class surface quality and low manufacturing costs. Most of the time, the metal parts are almost ready for installation.
Since both the models and the molds are lost during the casting process, this is referred to as casting from lost models and molds. The mold (negative model) is usually made of ceramic and is lost because it has to be destroyed after each casting in order to be able to demold the casting. The model (positive model), on the other hand, usually consists of wax or a polymer and depicts the desired piece of metal. It is dipped several times in form slip to maintain the ceramic shape. The wax model is lost during subsequent melting.
2. An overview of the lost wax process
1. Production of the wax injection mold
A mold or tool is required to map the contours of the investment casting component. This tool represents a negative image of the component and is usually made of aluminum or steel.
The shape itself must be worked precisely to ensure tolerances and surface quality.
2. Production of the wax model
The investment casting component is injection molded in mold wax. To do this, liquid wax is injected into the tool. The resulting wax model corresponds exactly to the later molded part.
The injection pressure of the machine and the temperature of the molding wax must be precisely coordinated to ensure high dimensional accuracy and surface quality.
3. Wax model assembly
The wax models are brought together using a wax tree or wax cluster. This is how the sprue system, which contains the feed channels to the mold, is created.
Experienced and trained investment casting experts carry out the assembly of the wax trees carefully and precisely in order to ensure high casting quality.
4. Diving, sanding & drying
By immersing the wax tree several times in form slip and then sanding and drying, a multilayer ceramic jacket is created.
The very high surface quality of the molded parts results from the first layer, which consists of fine-grained silicon sand.
5. Melting out
In this step of investment casting, the molding wax is melted out of the ceramic mold under pressure in a steam autoclave. Here, the wax model will be lost.
The wax is collected, processed and reused / recycled.
6. Burning
When the ceramic molds are fired, the last traces of the mold wax are burned off completely and without leaving any residue. This creates the necessary strength for investment casting.
When the ceramic molds are fired, the last traces of the wax are burned completely and without residue. This creates the necessary strength for the investment casting.
7. Investment casting
The metal alloy, which is customized for each casting batch when using the investment casting process, is melted in the induction furnace. The resulting molten steel is poured into the hot ceramic molds using a cast pan.
By precisely controlling the temperatures of the molten steel, casting ladle and ceramic molds, the investment casting process ensures a high quality of material and surface quality even with thin-walled components with complex geometries.
8. Mold removal
In the next step of the investment casting process, the ceramic shell is carefully removed after the pouring grape has cooled. More specifically, the ceramic mold is destroyed and lost in the process.
9. Disconnect
Now the cast component and cast stem / sprue system are carefully separated.
Here too, care is taken to re-use remaining steel residues in the next casting batch.
10. Radiation
The blasting process takes place in the penultimate step of the investment casting. It serves for the complete removal of the last ceramic residues on the surface of the cast parts.
Depending on customer requirements, the following steps then take place: sprue grinding, heat treatment, straightening process, mechanical processing and / or surface coating.
11. Final inspection
After all investment casting processes, we carry out a visual inspection at the production site.
The entire scope of all criteria and measures of quality control is coordinated in a functional manner depending on customer requirements.
3. Video: Process flow in the investment casting process
4. Origin of the investment casting process
Historically, the casting process is the origin of all procedures and dates back to around 3,000 BC. In the beginning, the lost wax process was used for casting art. For example, sculptures and bronze statues were created using the process.
The industrial use of investment casting began in the early 20th century with the manufacture of dentures by dentists and dental technicians. However, only low-melting metals could be cast at first.
In 1929, with the introduction of ethyl silicate as a binding agent, castings could also be made from high-melting alloys (cast steel).
Today, the casting materials are comprehensive. Investment casting is used throughout the industry.
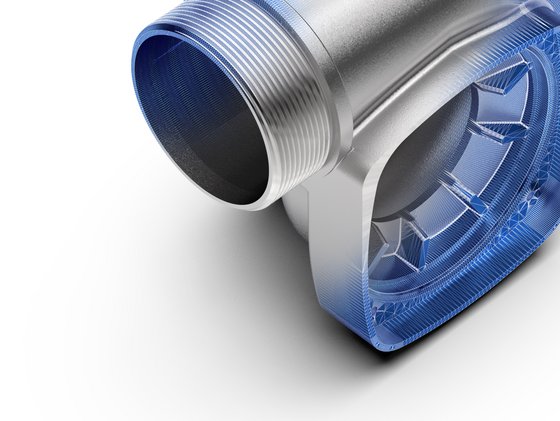
Do you need investment casting parts?
Find out more about the specifics of the investment casting process at Richter Formteile.
Service – to suit your needs
We see ourselves as your partner across the value chain!
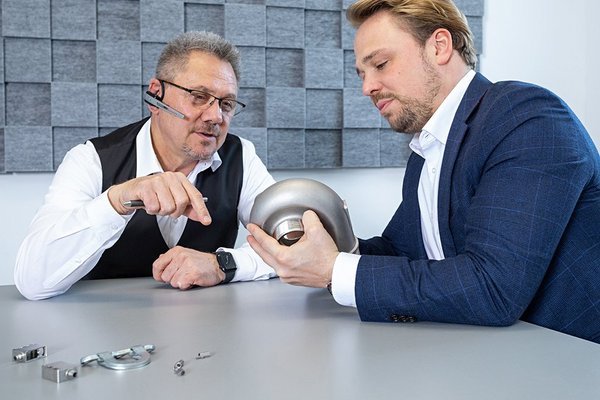
Technical Advice
We support you with your expert questions ✓ Coordinate your requirements and the technical drawings with our specialist staff!
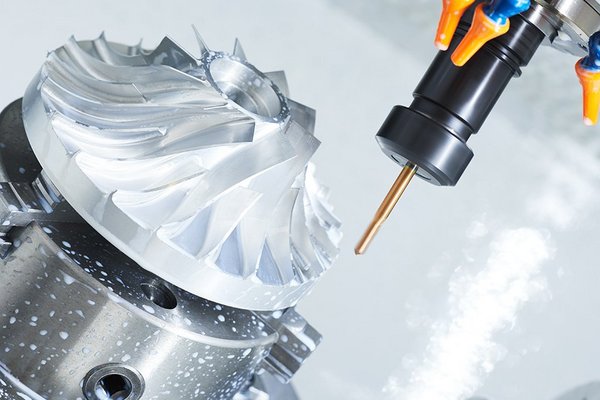
Processing / Assemblies
Extensive processing, surface treatment of metal parts ✓ pro-assembly and assembly of modules ✓ Tell us your requirements now!
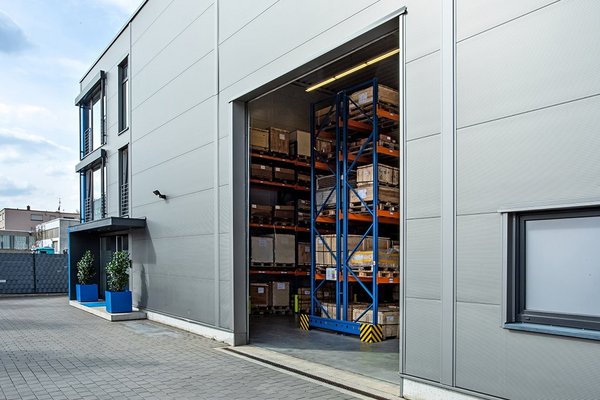
Supply chain management
In addition to the development and production of the components, we also take care of ✓ Procurement ✓ Logistics ✓ Customs clearance - Find out more and benefit from the advantages now!
5. Questions and answers about the investment casting process
FAQs on the investment casting process
Investment casting, also known as lost wax casting, is a precision casting process for the production of complex-shaped metal parts with high dimensional accuracy and fine surface quality. It is often used for applications in aviation, medical technology, jewelry manufacturing and mechanical engineering.
Investment casting offers high dimensional accuracy (±0.1 mm) with minimal post-processing, enables complex geometries and delivers smooth surfaces (Ra < 1.6 µm). It allows for a wide variety of materials, including steel, titanium and superalloys, and is ideal for series production with high repeat accuracy. The process saves material, reduces component weight and minimizes joints.
Comparison with other casting processes:
Investment casting is characterized by precision, surface quality and material variety, but is more cost-intensive than sand or die casting. It is particularly suitable for high-quality, delicate components in aviation, medical technology and automotive engineering.
A variety of metals and alloys can be used in investment casting, including:
- Steel and stainless steel
- Carbon steels, alloy steels, stainless steels (e.g. 304, 316)
- High strength, corrosion resistance, versatile in use
- Nickel-based alloys
- Inconel, Hastelloy, Monel
- Heat-resistant, ideal for turbine blades and high-temperature applications
- Titanium and titanium alloys
- Ti-6Al-4V (most common alloy)
- Lightweight, extremely strong, biocompatible (e.g. for medical technology, aviation)
- Aluminum and aluminum alloys
- AlSi alloys, AlCu alloys
- Lightweight, good thermal conductivity, corrosion-resistant
- Copper-based alloys
- Bronze, brass, copper-nickel alloys
- Good electrical/thermal conductivity, high corrosion resistance
- Cobalt-chromium alloys
- CoCrMo (e.g. for implants and dental technology)
- Wear-resistant, biocompatible, high-strength
This variety of materials makes investment casting particularly attractive for applications in aviation, medical technology, automotive engineering and mechanical engineering. Find out here which materials are processed at Richter Formteile.
In addition to the convincing advantages of the investment casting process, there are the following limitations and disadvantages that need to be considered:
- High costs
- The production of wax models and ceramic molds is complex and expensive.
- The tool costs can be uneconomical, especially for small quantities.
- Longer production times
- The multi-stage process (model creation, mold production, casting, demolding) requires more time than other casting processes such as sand or die casting.
- Limited component size
- Investment casting is mainly suitable for small to medium-sized components (a few grams to a few kilograms).
- Very large components are often uneconomical or technically difficult to produce.
- Sensitivity of the ceramic mold
- The ceramic mold can break during casting, especially with very thin or complex structures.
- Material limitations
- Although many metals can be used, some materials with extremely high melting temperatures or reactivity (e.g. pure tungsten alloys) are difficult to process.
Despite these limitations, investment casting remains the preferred choice for high-precision, complex and high-quality metal parts.
The investment casting process is particularly suitable for applications that require high precision, complex geometries and high-quality materials. Typical areas of application are:
- Aerospace
- Turbine blades, engine components, structural components
- Heat-resistant nickel and titanium alloys for extreme loads
- Medical technology
- Implants (e.g. hip joints, dental implants), surgical instruments
- Biocompatible materials such as titanium or cobalt-chrome
- Automotive industry
- Engine and chassis components, turbocharger housings, pump housings
- High dimensional accuracy and material savings for lighter components
- Mechanical engineering & industry
- Valves, pumps, precision gears, tools
- High wear resistance and corrosion resistance
- Jewelry and watch industry
- Fine, filigree designs made of gold, silver, platinum
- Detailed structures without complex post-processing
- Energy & power plant technology
- Turbine components, high-performance fittings
- High-temperature resistant materials for extreme conditions
Investment casting is used wherever high-precision, delicate and durable metal parts are required.
Investment casting offers very high precision compared to other casting processes. The most important dimensional accuracies are:
- Dimensional tolerances
- Typical dimensional accuracy of approx. +/- 0.7 % of the nominal dimension.
- The geometry and component size have a major influence on achievable tolerances.
- Surface quality
- Roughness (Ra) of 6.3 µm, depending on the material and mold condition.
- Much smoother than sand casting, but often requires light finishing if high-gloss surfaces are required.
- Repeatability
- The wax model and standardized process ensure consistent results in series production.
- This is particularly advantageous for components with complex internal structures or thin wall thicknesses.
Investment casting is particularly precise and ideal for complex geometries. For absolute high precision, post-processing such as grinding or milling may be necessary.