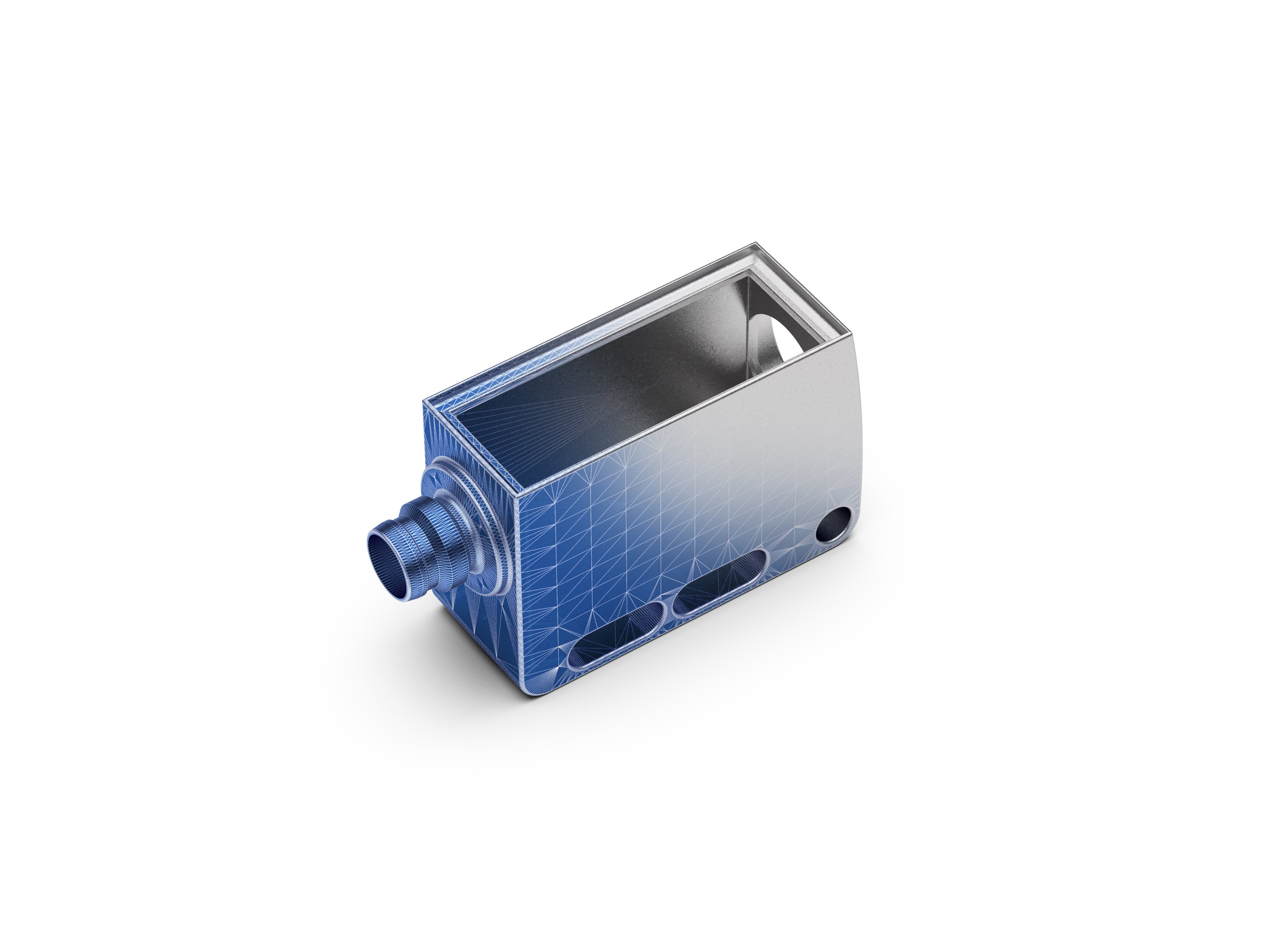
MIM Procedure
1. Definition
MIM technology, also known as metal injection molding, combines two technologies: injection molding (known from plastic injection molding) and sintering technology.
Due to the implementation of high geometrically complex requirements already in the production process, this technology is referred to as a near-contour manufacturing process.
In this molding process, fine metal powder and thermoplastic polymer resin are mixed in order to obtain a sprayable granulate, the feedstock. The green body obtained in this way is released after cooling in order to detach the plastic. The resulting component, also known as brown body, has a porous surface and is therefore sintered just below the melting temperature.
The advantage of the MIM process is the diverse selection of shaping options and materials. MIM technology is particularly suitable for the production of small and medium-sized metal parts of complex geometry in medium and large series.
While in other processes several components have to be produced separately and assembled to form a component group, one component can be made in one piece in the MIM process. Also bores, threads, undercuts, engravings, and much more can be produced in one production step.
2. An overview of the MIM procedure
1. Mix
In the first step of MIM technology, the fine metal powder is kneaded and heated according to its desired alloy with thermoplastic material as a binder to form a homogeneous powder mixture.
2. Feedstock
After granulation, the metal mixture – the feedstock – is viscous and can now be processed in the injection molding process.
3. Injection molding
At elevated temperature, the feedstock is now injected into a closed mold at high pressure. The form is first filled in completely and then plasticized.
The resulting green body has all the geometric properties of the finished component.
4. Debinding
The cooled green body is now removed from the injection molding machine. The binder is removed in a two-stage process, thermal or catalytic debinding. This can take up to 24 hours.
What remains is a purely metallic, but still open-pore component, the so-called brown body.
5. Sintering
n order to make a precision molded part with the desired geometric and mechanical properties out of the brown body, it has to be sintered at high temperatures.
The molded part can then be treated further if necessary.
6. Final inspection
All our parts are subjected to a comprehensive visual inspection after the MIM process has been completed.
The entire scope of all criteria and measures of quality control is coordinated in a functional manner depending on customer requirements.
3. Video: Process flow in the MIM procedure
4. Origin of metal injection molding
MIM technology has been known for almost a century: The first ceramic housings for spark plugs were already produced in 1920 using metal powder injection molding.
The MIM process did not really arrive in industry until 1980. Initially, MIM was used to produce small, high-precision metallic molded parts for industrial goods.
In the meantime, MIM technology has become indispensable in industry. The MIM process has established itself as a highly economical manufacturing process for large series products, which is used particularly in case of high complexity.
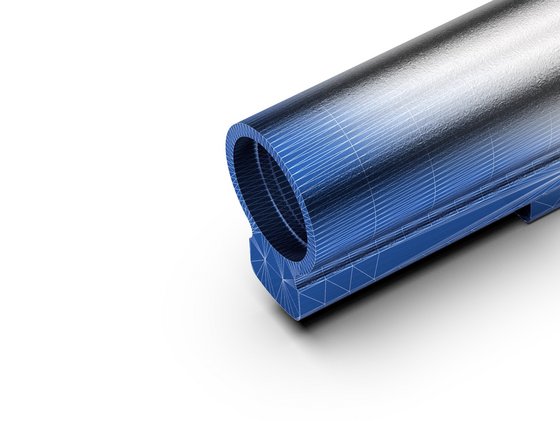
Do you need MIM-parts?
Find out about the specifics of the MIM process at Richter Formteile here.
Service – to suit your needs
We see ourselves as your partner across the value chain.
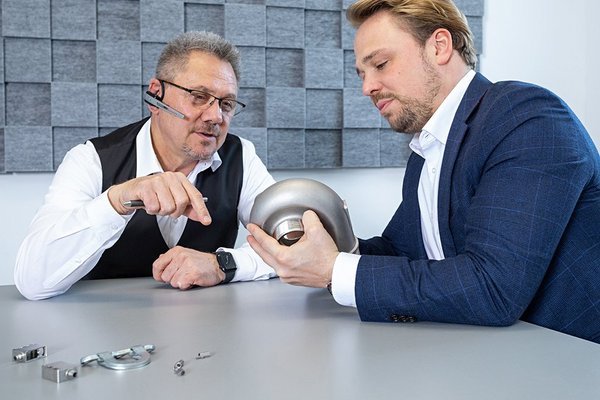
Technical Advice
We support you with your expert questions ✓ Coordinate your requirements and the technical drawings with our specialist staff!
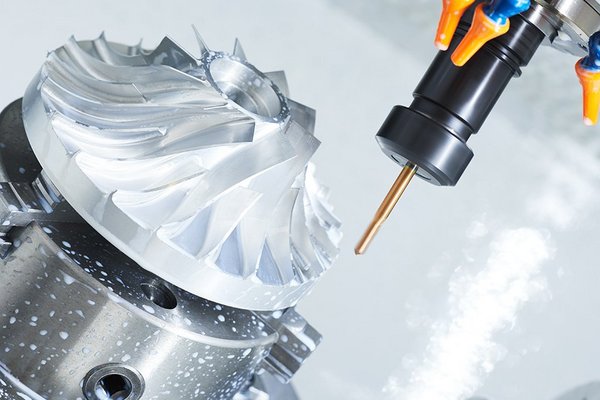
Processing / Assemblies
Extensive processing, surface treatment of metal parts ✓ pro-assembly and assembly of modules ✓ Tell us your requirements now!
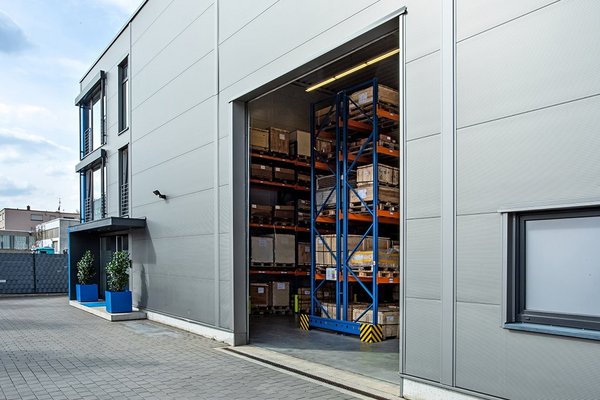
Supply chain management
In addition to the development and production of the components, we also take care of ✓ Procurement ✓ Logistics ✓ Customs clearance - Find out more and benefit from the advantages now!
5. Questions and answers about the MIM manufacturing process
FAQs on the MIM process
MIM stands for Metal Injection Molding. It is a manufacturing process that combines the advantages of plastic injection molding technology with metal processing.
MIM enables the production of complex, precise metal parts by injecting a mixture of metal powder and plastic into a mold. After injection molding, the binder is removed and the component is sintered, giving it its final strength.
MIM is particularly suitable for small, high-precision metal parts in medical technology, the automotive industry, aviation and electronics.
The metal injection molding (MIM) process is particularly suitable for complex, small-format metal parts with high precision. Typical areas of application and classic components that are produced using the MIM process include:
- Automotive industry
- Gear wheels & gears
- Valve parts
- Injection system components
- Sensor and actuator housings
- Shift and clutch components
- Medical technology
- Surgical instruments (e.g. forceps, scissors)
- Minimally invasive surgical tools
- Dental implant components
- Endoscopic components
- Watch and jewelry industry
- High-precision watch movements & gear wheels
- Clasps for bracelets
- Decorative metal parts with complex designs
- Aerospace industry
- Small components for jet engines
- Structural components with high temperature resistance
- Sensor housings
- Electronics & telecommunications
- Smartphone & laptop housings
- Connectors & contact pins
- Heat sinks
- Weapons and security industry
- trigger mechanisms
- Locking systems
- Safety elements
MIM is particularly suitable for components that require high strength, complicated geometries and fine structures. It is particularly advantageous for large quantities, as it is more cost-efficient than machining production processes.
The MIM process (Metal Injection Molding) offers numerous advantages:
- High design freedom - complex geometries, thin walls, functional integration.
- Excellent material properties - high strength, density (95-98%), variety of materials (stainless steel, titanium, tungsten, etc.).
- High precision - Tight tolerances (approx. +/- 0.3 % of nominal dimension), hardly any reworking necessary.
- Efficient mass production - Cost-saving, low material loss, ideal for high quantities.
- High-quality surfaces - Fine structures, low roughness (Ra 3.2 µm).
- Sustainability - Material recycling & energy-efficient production.
- Perfect for small & delicate components - Ideal for medical technology, automotive & electronics.
MIM combines the design freedom of injection molding with the strength of metal - ideal for precise, complex components in series production.
The MIM process (Metal Injection Molding) differs from CNC machining and casting in several aspects. Here are the most important differences:
- Geometric complexity
- MIM: Enables highly complex shapes, undercuts and thin-walled structures without additional machining.
- CNC: Limited design freedom, complex shapes require additional machining steps.
- Casting: Good variety of shapes, but not as precise as MIM and often involves post-processing.
- Precision & tolerances
- MIM: High dimensional accuracy, often no post-processing required.
- CNC: Extremely high precision (down to the micrometer range), ideal for individual parts and small batches.
- Casting: Lower dimensional accuracy, often requires post-processing.
- Material selection & properties
- MIM: High density, very good mechanical properties comparable to rolled or forged metal.
- CNC: Uses solid metal blocks, therefore best material properties, but high material loss.
- Casting: Can be more brittle (pores, shrinkage cavities), mechanical properties often worse than MIM.
- Cost-effectiveness & series production
- MIM: Particularly cost-effective for large quantities (series production).
- CNC: High costs for large quantities, but ideal for individual parts and prototypes.
- Casting: Suitable for large components and high quantities, but often associated with post-processing costs.
- Sustainability & material efficiency
- MIM: Very low material loss as metal powder can be reused.
- CNC: High material loss due to chip removal.
- Casting: Material utilization better than CNC, but not as efficient as MIM.
Conclusion:
- MIM is suitable for small, complex components in large quantities.
- CNC machining is ideal for high-precision individual parts & small batches.
- Casting is advantageous for large, less complex components.
The metal injection molding (MIM) process is used in many industries, especially where complex, precise and high-strength metal components are required in large quantities.
- Automotive industry
- Gear wheels, transmission gears, clutch parts
- Injection systems, sensor & actuator housings
- Lock mechanisms, electrical contacts
- Medical technology
- Surgical instruments (forceps, scissors)
- Minimally invasive surgical tools
- Dental implants & orthodontic components
- Aerospace
- Small components for engines & turbines
- Structural components with high temperature resistance
- Sensor & actuator housings
- Watch & jewelry industry
- Precise watch movements, gear wheels, springs
- High-quality housings & bracelet clasps
- Decorative metal elements
- Electronics & telecommunications
- Connectors, electrical contacts
- Heat sinks for microchips
- Smartphone & laptop housings
- Weapons & security industry
- Trigger mechanisms, safety elements
- Housings for optical & electronic target systems
- Industrial applications
- Cutting tools, knives & blades
- Pump parts, valves, bearings
- High-precision mechanical components
MIM is particularly attractive for industries that require small, complex and heavy-duty metal parts in large quantities and with high precision.