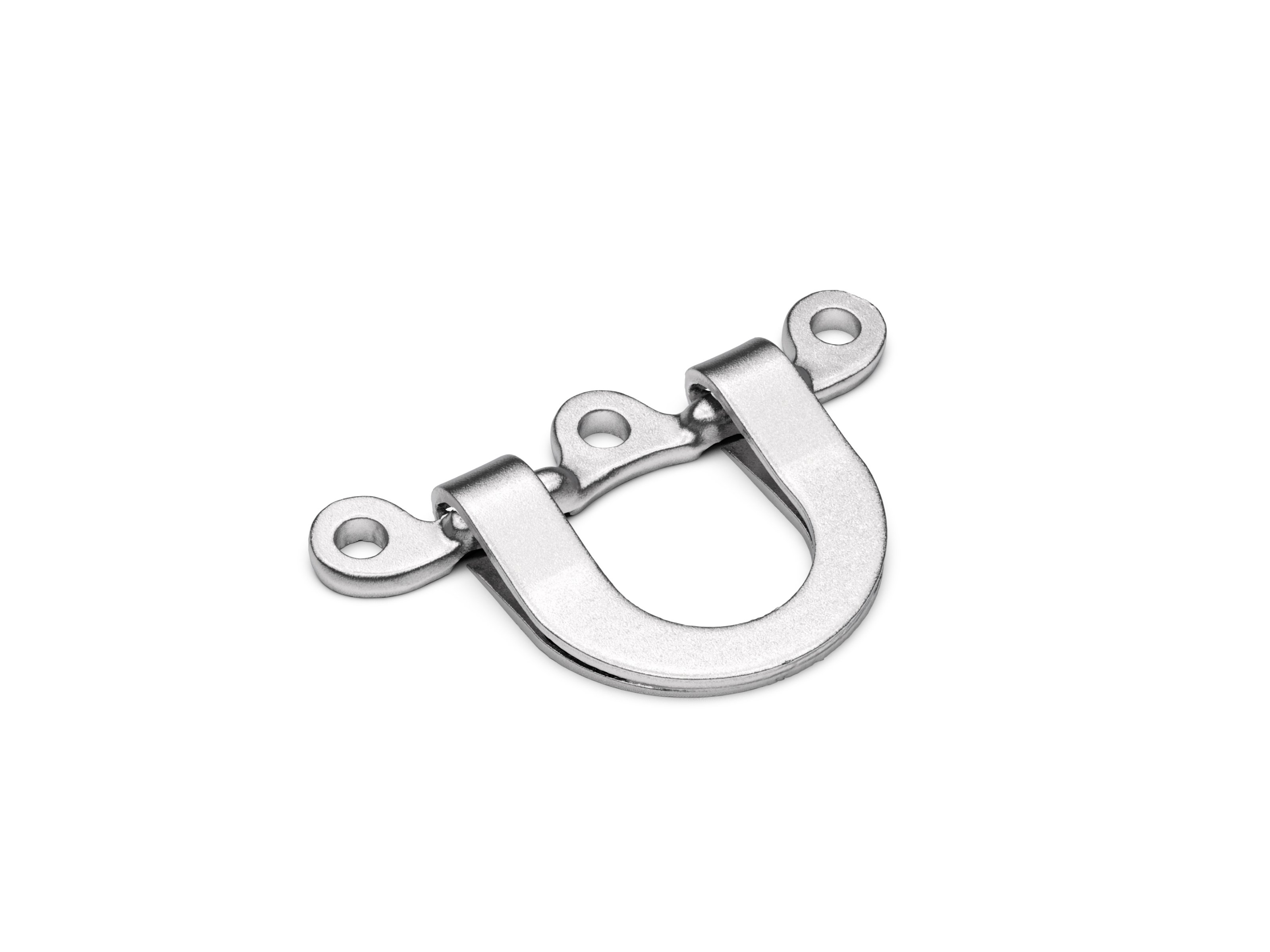
Die forging process
Table of Contents
1. What is a drop forge?
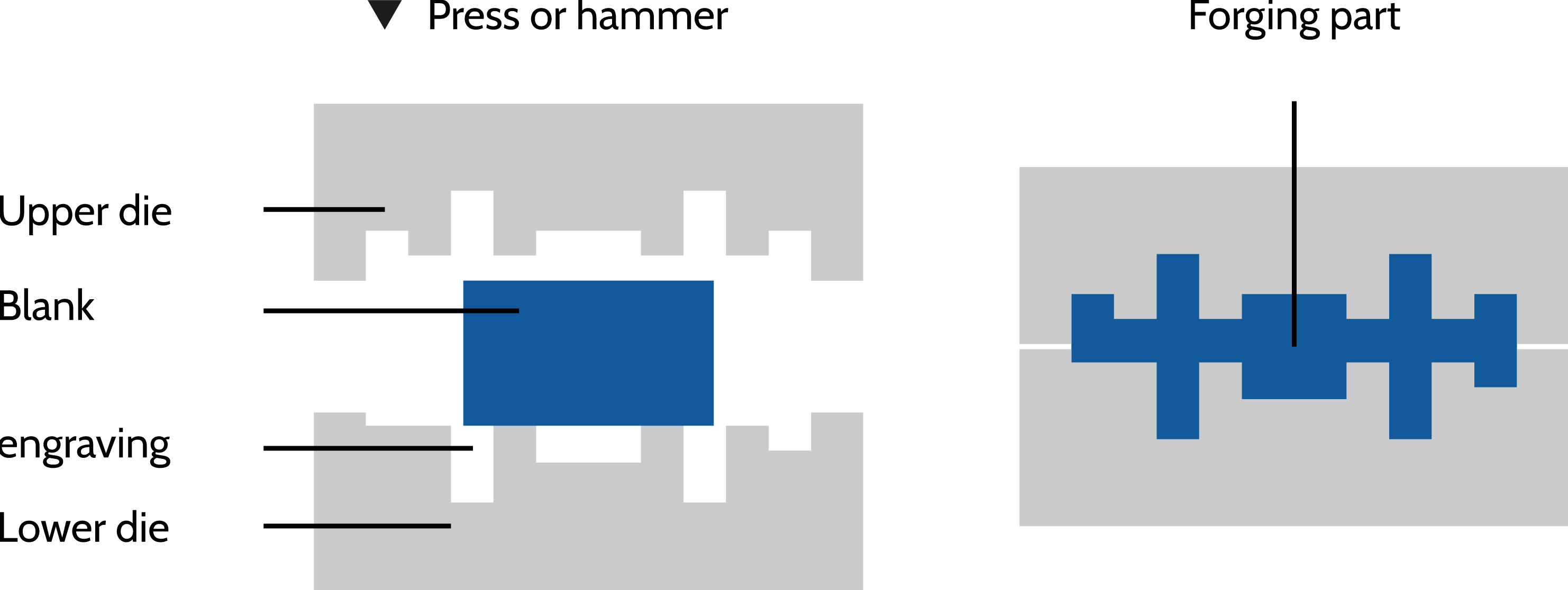
Die forging or die forming is a manufacturing process, more precisely a forming process or solid forming process, and comes from the main group of forming. There it is assigned to the group of pressure forming together with rolling, free-forming, indenting and spinning. According to DIN 8583, it is a pressure forming process in which forming tools move against each other, the dies.
The tool contains the engraving of the moulded part to be produced as a negative and consists of an upper and lower die. The dies are moved against each other with great force under the action of a press or hammer, thus working the material into the desired shape.
The forged pieces convince with a homogeneous, dense grain, which has neither pores nor other cavities.
In principle, drop forging is the most widely used forging method. It is used, for example, to produce aircraft, ship or car parts, as well as for constructions and the manufacture of various industrial products.
1.1 Die moulds
The main distinction between drop forging with burr and drop forging without burr is that it is a die forging process. Both forms belong to the group of die forging with a completely enclosed workpiece.
In drop forging with burr, the excess material is forced into the burr gap of the engraving; the so-called burr. The deburring, i.e. the removal of the excess material, is carried out with the help of additional tools that act like a kind of punch.
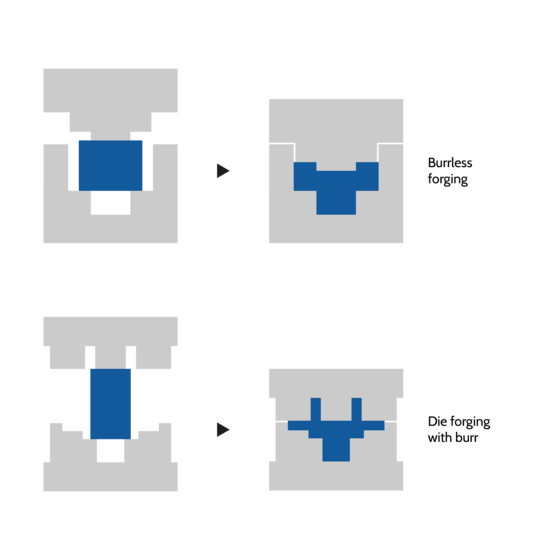
In closed die forging, the engraving is in one half of the die and the second half goes into the first. There is no burr formation in this case, which is why this type of drop forging is also called "burrless forging". Since there is no burr, this precision forging is characterised in particular by no or very little excess material. However, the removal of the shaped part requires a particularly high amount of force in the forging process.
In addition to the above-mentioned drop forging with a completely enclosed workpiece, drop forging can consequently also be subdivided into drop forging with a partially enclosed workpiece.
1.2 Subdivision forms of drop forging
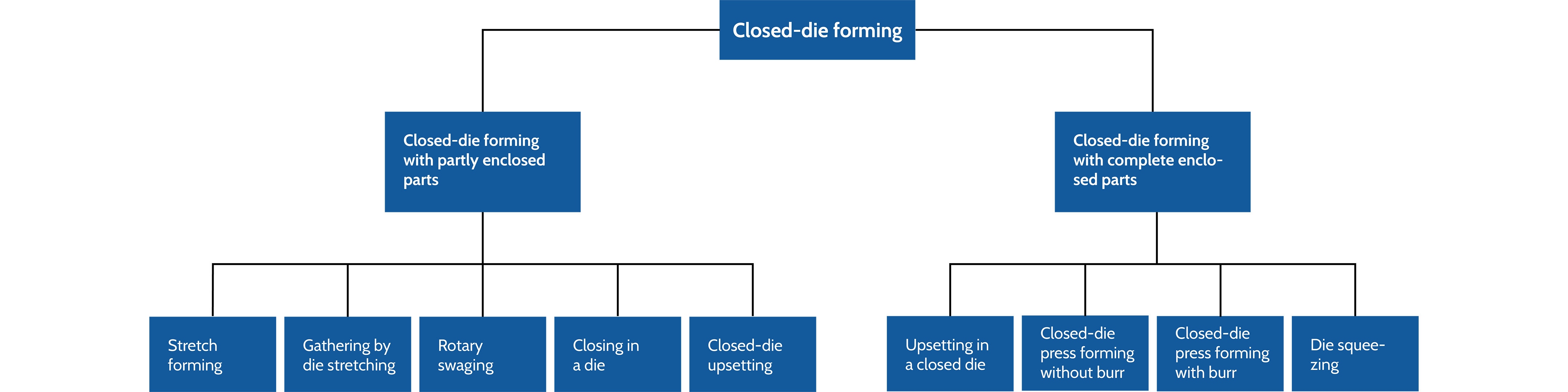
drop forging "from the metal bar"
Forging from the bar is associated with die forming with a partially enclosed workpiece. As a rule, about 2 m long rolling bars are used here, which are heated at one end, forged in a drop and then the workpiece is separated from the bar with a hammer blow.
The advantage of drop forging from the bar lies in the simple handling, as the workpiece does not have to be clamped. However, the use of materials is higher, which is a disadvantage. This process is used when workpieces are to be forged in an elongated form weighing up to 3 kg and bar diameters of up to 50 mm.
Sub-forms of die forming with a partially closed workpiece are form stretching, stretch upsetting, rotary swaging, closing in the die and form upsetting.
drop forging "from the piece"
Forging from a piece involves die forming with a completely enclosed workpiece. Here, either a sheared or sawn-off bar section is used as the starting blank. The advantage of drop forging from one piece is that the fiber flow optimally follows the outer contour. The greater use of material can be seen as a disadvantage.
The piece can be drop forged either with or without a burr. In industrial practice, drop forging with a burr is the shaping process that is primarily used.
With regard to filling the die engravings, a distinction is made between three basic types of filling processes:
- Upsetting: The material flow mainly runs parallel to the tool movement.
- Widths: The material flow is mainly perpendicular to the tool movement.
- Rising: The material flow runs parallel against the tool movement.
Unlike forging with a burr, the workpiece is completely enclosed by the tool when forging without a burr, so no material escapes. The rest of the forming process is analogous to that with a burr.
forging "from the split piece"
The forging of the split piece can ultimately be assigned to both die shapes, with a fully and partially enclosed die.
The drop forging of the split piece is based on an initial shape that is cut out of a strip of sheet metal, whereby this process takes place by surface closure and the sheet metal strips are cut to size with almost no loss. An intermediate shape is created by bending or upsetting and the workpiece is then given its final shape in the die.
Drop forging from split pieces is primarily suitable for flat and small workpieces, with the clear advantage being low material consumption and short forging times. The disadvantage is the fiber flow, which cannot be ideally adapted to the shape of the workpiece, which can lead to an impairment of the reverse bending strength.
This process is primarily used for mass-produced parts such as wrenches, pliers, scissors or knives that do not have to meet particularly high strength requirements.
1.3 Differentiation: Hot, semi-hot and cold forming in production
In production, a distinction is made between hot, semi-hot and cold forming. Die forming is usually carried out at workpiece temperatures above the recrystallisation temperature, which is why it is also called hot forming. Here the workpiece is heated in the furnace to the required forging temperature so that the metal becomes soft. This allows the production of forged parts of the most complicated shapes: Wheel carriers, crankshafts, steering knuckles, connecting rods, gear wheels, turbine blades, etc..
In principle, all metals that can be kneaded after heating are suitable for use in drop forging. Most drop forgings are still made of steel, but aluminium is gaining in importance.
However, aluminium is becoming more and more important as a light metal or other alloys. For example, aluminium forging is often used in the automotive industry.
Cold forging in the die produces precise and high-quality parts. Since the workpiece is not subjected to any preparatory heating, there is no temperature expansion, scaling or thermal defects. Nevertheless, cold forging in the die is used less frequently because most metals and their alloys have a high strength in the cold state and machines with very high power are required for their deformation.
2. Drop forging processes
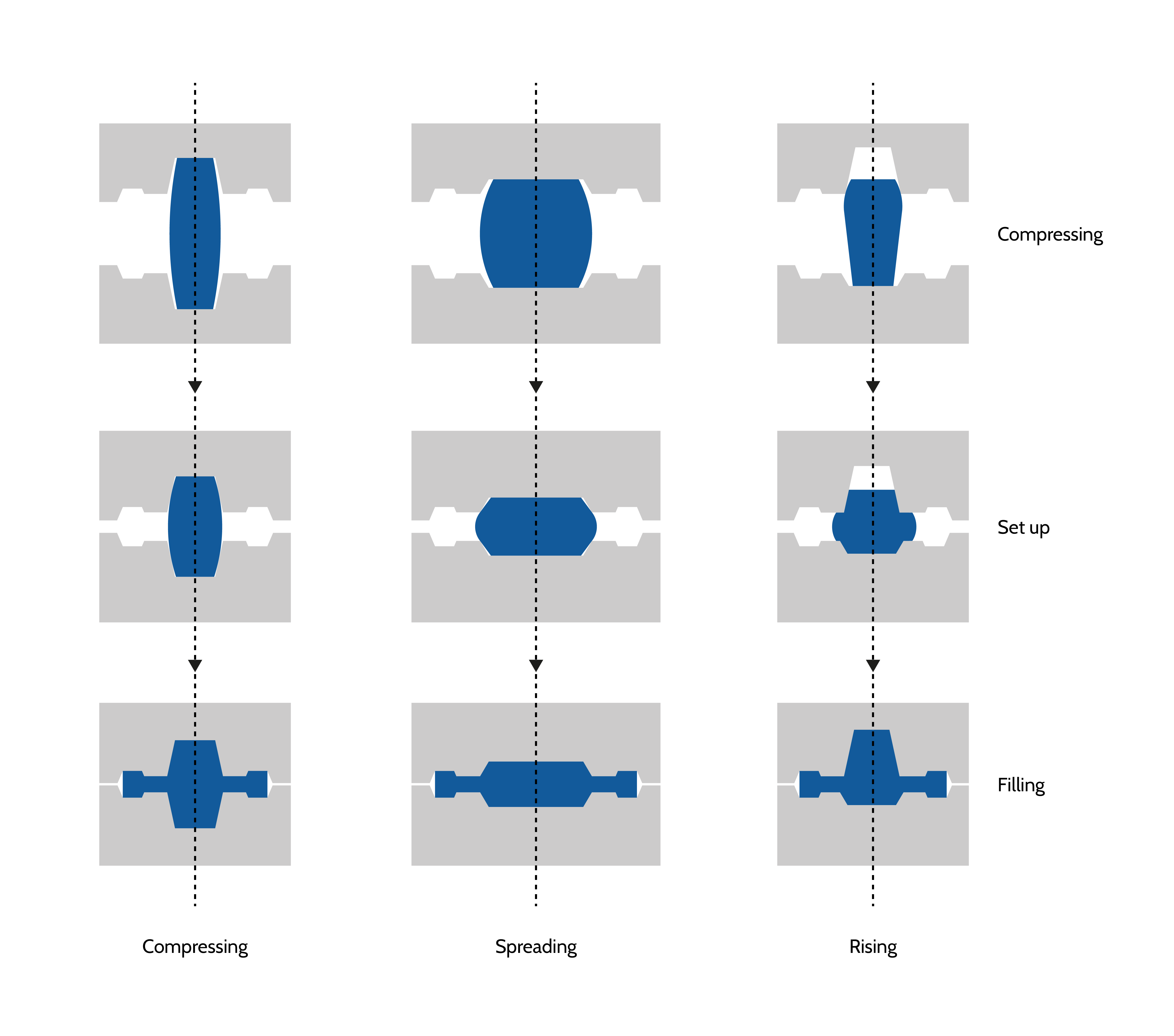
The filling of the die engraving within the closed-die forging takes place according to the three basic processes of guided material displacement, of which at least two occur during a closed-die forging process:
- In upsetting, the essential flow of material occurs parallel to the movement of the die, and the initial height is reduced.
- In the case of widening, the material is displaced laterally, whereby this occurs from the inside to the outside. The main flow of material during spreading is perpendicular to the movement of the tool.
- During rising, deep engraving cavities are filled, whereby the essential material flow takes place parallel against the movement of the tool.
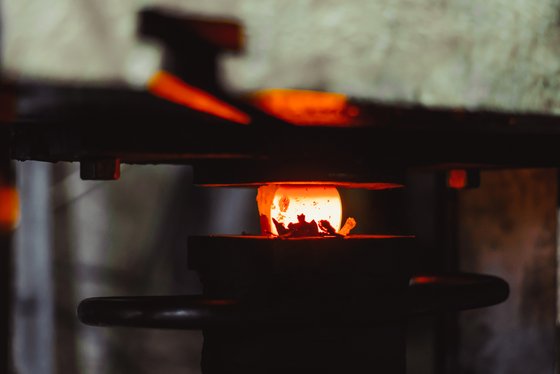
The transitions of the material displacement usually occur smoothly. A compressive stress is applied to the workpiece, which is generated by the upper and lower tool (or upper and lower die). More precisely, this pressure is triggered by a forming machine, the press (see Fig. 1).
The components to be formed are heated in advance so that the compressive stresses and the loads on the tools do not become too strong. In general, almost all formable materials can be forged in the die.
Steel is usually heated to 1,000 °C to 1,280 °C for forming the components. Materials such as magnesium, aluminium, stainless steel, brass, copper and their alloys can also be used for drop forging.
3. The drop forging process
1. Warming
The first step consists of separating the blank from the semi-finished product, which is brought to the required temperature for forming in the furnace.
Various systems are used for heating, which heat the workpiece in such a way that the temperature is above the austenitization temperature of the respective material. The following systems are used: inductive heating systems, conductive heating systems, natural gas-powered chamber furnaces.
2. Forging process
First, the blank is separated from the semi-finished product and brought to the workpiece temperature.
With the help of rollers, presses or an air hammer, the heated blank is preformed if necessary.
3. Forging process
In the next step of the forging process, the blank is placed in a closed die.
The upper and lower dies contain the contour of the desired forging as a negative and press the blank into the appropriate shape with several strokes.
Excess material is pushed into the ridge.
4. Deburring
During this step, the protruding burr is removed (deburring). Specific deburring tools are used for this. If necessary, this work step can be supplemented by punching the workpiece.
After the forging has been completed, it is possible to reshape it using the die.
5. Tempering of drop forgings
This is followed by the final tempering (heat treatment) of the forgings in furnaces.
6. Descaling
The scale layer created is now mechanically removed from the forging.
7. Final inspection
After the forging process has been completed, all precision molded parts in metal forming technology are subjected to a comprehensive visual inspection.
The entire scope of all criteria and measures of quality control is coordinated in a functional manner depending on customer requirements.
4. Video: Process flow in drop forging
5. Advantages and disadvantages
Advantages of drop forging
During the rolling of the starting material or during the drop forging itself, defects such as pores and blowholes, which often occur in the production of cast parts, are closed. As a result, forged parts are more stable than cast parts with the same or even lower weight.
Compared to machined components, forged parts have a grain structure that is adapted to the forming process. This means that the grain of the machined component is broken (see Figure 5). This results in a high static and dynamic resilience of drop-forged parts, since they can be perfectly adapted to their demands.
Disadvantages of drop forging
The type of process chosen determines the disadvantages of drop forging. The complex die design and the excess material required for the shaping occur in drop forging with a burr.
When drop forging without a burr, the necessary precision causes disadvantages, since the construction of the dies is even more complex than for drop forging with a burr. Compliance with very small tolerances within the process also causes a great deal of effort. Overloading of the die due to volume fluctuations in the pre-products quickly leads to tool failure or to an incompletely filled engraving. This manufacturing method is not suitable for the manufacture of workpieces with a complicated geometry.
6. Grain flow in forging compared to alternative methods
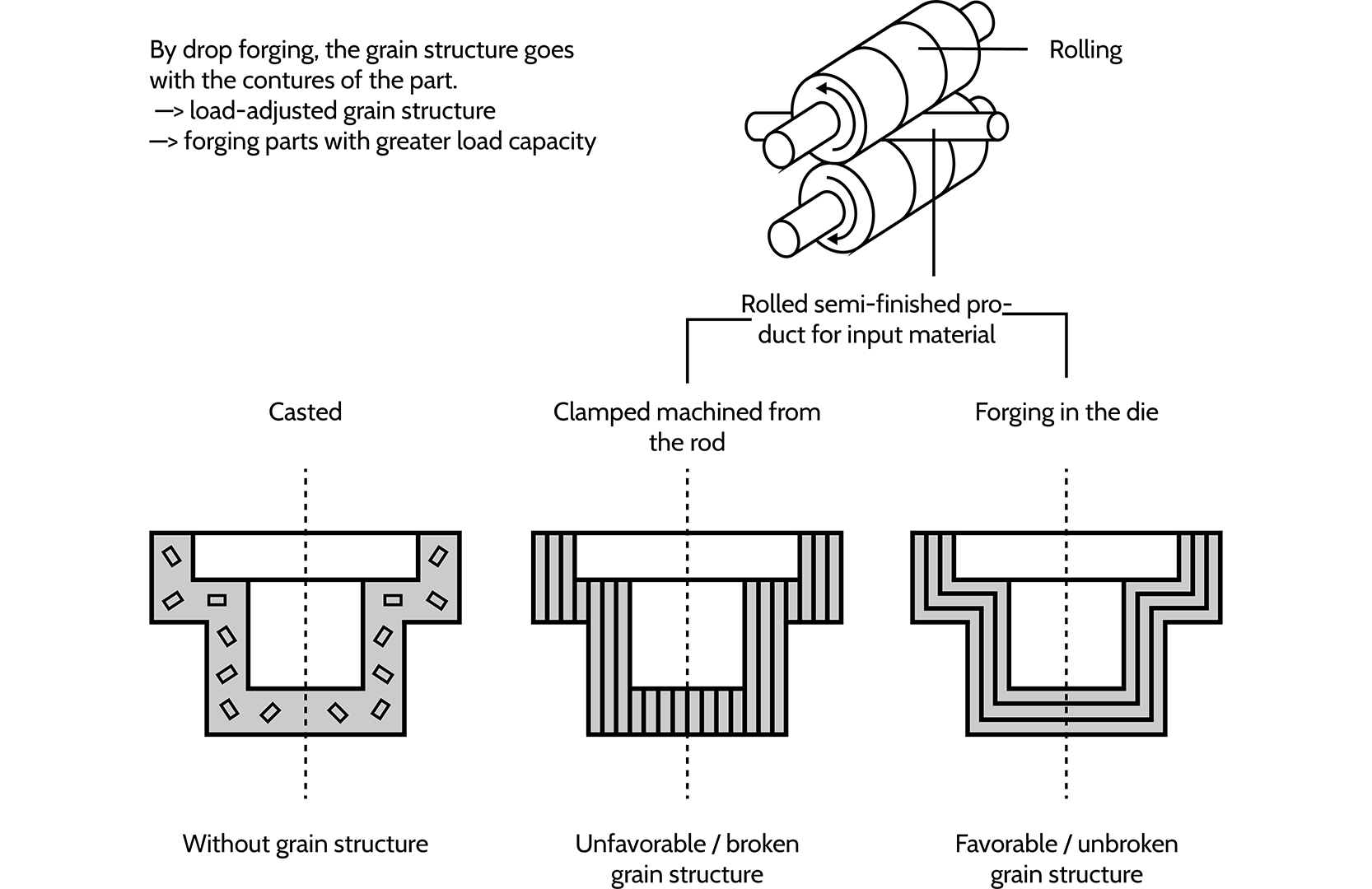
7. Origin and history
The forging process has been used since 1,500 BC. At that time, drop forging involved placing the blank in the die and hammering it into shape. Although the forming technique was continuously developed in the following years, it was not until the end of the 19th century that modern drop forging tools were produced in England.
This progress was greatly aided by the development of the steam hammer, which now made it possible to forge large parts. As the 20th century progressed, the achievable precision in drop forging also became higher and higher. Modern developments also aim at a higher degree of automation of the forging process.
8. Wide range of applications
Drop forging is suitable for the mass production of individual workpieces, which can weigh a few grams or several tonnes. A wide range of dimensions and series sizes is also possible: from a few centimetres to several metres, or from just a few pieces to several million.
Drop forging is suitable for the production of structural parts for machines such as aircraft or vehicles. But it is also used to produce tools such as spanners, pliers or hammers.
The automotive industry, the two-wheeler industry, mechanical engineering as well as the railway industry, mining, shipbuilding and the aircraft industry are the main customers in Germany for workpieces produced by drop forging.
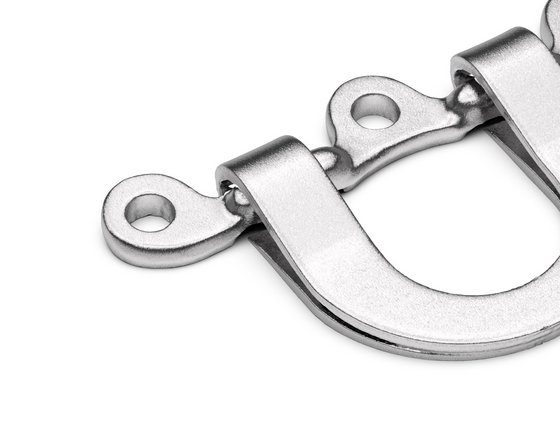
Do you need drop forging parts?
Find out more about the specifics of the drop forging process at Richter Formteile here.
Service – to suit your needs
We see ourselves as your partner across the value chain.
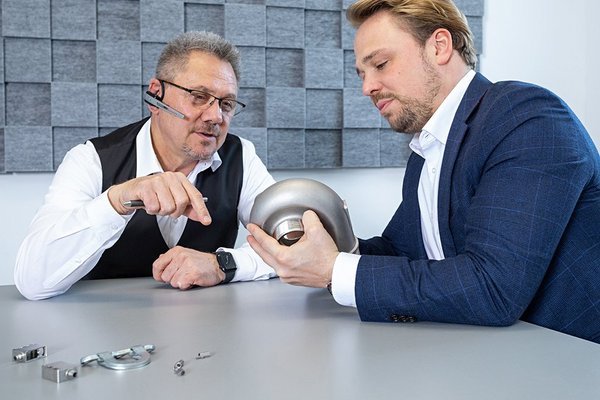
Technical Advice
We support you with your expert questions ✓ Coordinate your requirements and the technical drawings with our specialist staff!
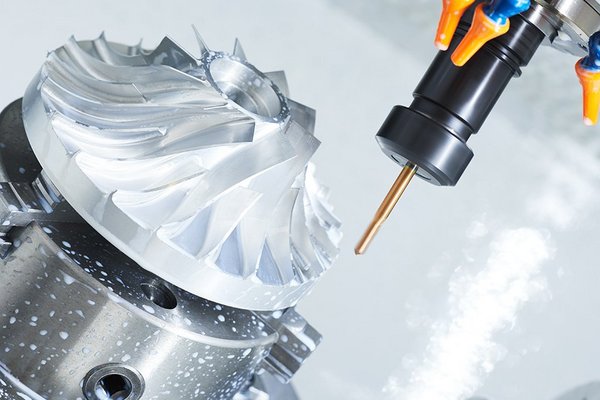
Processing / Assemblies
Extensive processing, surface treatment of metal parts ✓ pro-assembly and assembly of modules ✓ Tell us your requirements now!
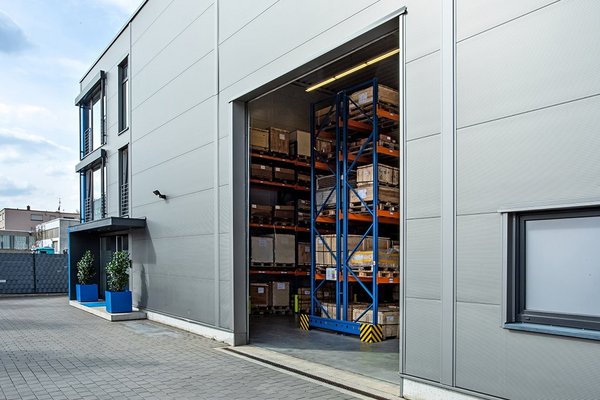
Supply chain management
In addition to the development and production of the components, we also take care of ✓ Procurement ✓ Logistics ✓ Customs clearance - Find out more and benefit from the advantages now!
9. Questions and answers on the subject of drop forging
FAQs on drop forging
In a drop forge, drop forging is used as a manufacturing process. In this process, a heated piece of metal (usually steel, aluminum or brass) is pressed between two specially shaped dies (tool moulds) to give it the desired shape.
Features of drop forging:
- High precision: The die creates an exact, repeatable shape.
- High strength: Forging improves the material properties as the structure is compacted and fibers are aligned in the desired direction.
- Series production: Ideal for the production of large quantities, e.g. for automotive, mechanical engineering or aerospace parts.
- Various processes: There are hot, warm and cold forging processes, with hot and warm processes being the most commonly used.
Applications:
- Crankshafts
- Connecting rods
- Gear wheels
- Tools (e.g. wrenches, hammers)
- Chassis components in the automotive industry
Drop forging is an important process in metalworking as it enables robust and highly resilient components.
Die forging is a forming manufacturing process in which a heated piece of metal (usually steel, aluminum or brass) is pressed into a specific shape between two dies. The dies are special tools with a hollow shape that shape the workpiece into the desired geometry during forging.
This process is used to produce high-strength and precise components for various industries, including automotive, aerospace, mechanical engineering and tool manufacturing.
How does drop forging work? The process consists of several steps:
1. Heating the workpiece
- The raw material (e.g. steel, aluminum) is heated to a high temperature.
- In hot drop forging, this is often 1,100-1,300 °C for steel.
2. Preforming (optional)
- In some cases, the metal is brought into a rough shape by rolling or pre-pressing.
3. Die forging
- The heated workpiece is placed between two dies.
- A press or hammer exerts high forces, causing the metal to flow into the desired shape.
4. Burr removal
- Excess material (the burr) is removed after forging.
5. Heat treatment (optional)
- Heat treatment can be carried out to improve the material properties (e.g. hardness, toughness).
6. Finishing
- If necessary, the component is cut to size by turning, milling or grinding.
Drop forging is therefore an indispensable process for high-quality metal parts with high strength and precision.
Forging is generally understood to mean open-die forging. In other words, forging without a die/tool mold. This type of forging is well suited for individual parts that need to be manufactured flexibly. Forging in a die, on the other hand, enables high precision and is therefore very suitable for series production.
- Forged (open-die forging)
- Shaping by targeted blows or pressure, without a fixed shape.
- Flexible, but less precise.
- Ideal for individual pieces (e.g. large shafts, turbine parts).
- Drop forged (die forging)
- Metal is pressed into a prefabricated die.
- High precision, ideal for series production (e.g. gear wheels, connecting rods).
- Higher tool costs, but economical for large quantities.
Metals with good formability at high temperatures are particularly suitable for drop forging. Frequently used materials are:
- Steels (most frequently used)
- Carbon steels (e.g. C45, C60) - high strength, good forgeability
- Alloyed steels (e.g. 42CrMo4, 34CrNiMo6) - for highly stressed components
- Stainless steels (e.g. 1.4301, 1.4542) - corrosion-resistant, but more difficult to forge
- Aluminum alloys
- Lightweight, corrosion-resistant
- Used in aviation, automotive engineering, mechanical engineering
- Examples: AlMgSi1, AlCu4Mg1
- Copper and brass alloys
- Good electrical conductivity, corrosion resistance
- Used for fittings, electrical engineering, pipe connections
- Examples: CuZn40, CuAl10Ni5Fe4
- Titanium alloys
- Extremely light and strong, heat-resistant
- Used in aviation and medical technology
- Example: Ti6Al4V
- Nickel-based alloys
- High temperature and corrosion resistance
- Used in turbines, aerospace, chemical industry
- Example: Inconel 718
Summary:
- Steels → most commonly used, high strength
- Aluminum → lightweight, for aviation/cars
- Copper/brass → good conductivity
- Titanium/nickel → for extreme conditions
Click here to find out which materials are available from Richter Formteile.
Drop forging is used in many industries, especially where high-strength, precisely formed metal components are required. The most important industries include
- Automotive industry
- Manufacture of crankshafts, connecting rods, gears, steering knuckles and steering components.
- Drop-forged parts offer high strength and durability, which is crucial in vehicles.
- Aerospace
- Production of engine components, chassis components and structural components.
- Lightweight but extremely strong components are essential here.
- Railroad industry
- Forged parts for wheelsets, axles, couplings and chassis components.
- Necessary for high loads and a long service life.
- Mechanical and plant engineering
- Heavy-duty tools, shafts, gear wheels, bearings and connecting elements.
- Necessary for use in heavy machinery.
- Oil and gas industry
- High-pressure valves, drilling tools, flanges and pump components.
- Forged parts withstand extreme temperatures and pressures.
- Agricultural and construction machinery
- Manufacture of axles, gears, blades and other high-strength components.
- Required for robust and durable machines.
- Energy industry (power plants & wind turbines)
- Turbine shafts, generator components, flanges and connecting elements.
- High stress due to mechanical and thermal loads.
- Medical technology
- Production of surgical instruments and prosthetic components.
- High-precision, corrosion-resistant and biocompatible materials are in demand.
Drop forging is therefore irreplaceable in many branches of industry, as it delivers components with high strength, precision and durability.
Drop forging offers several advantages over other forging processes, particularly in terms of precision, efficiency and material properties. Here are the most important advantages compared to other forging processes:
- Homogeneous microstructure - high load capacity and strength.
- High dimensional accuracy & repeatability - Precise shapes reduce reworking.
- Higher strength - optimized grain flow improves mechanical properties.
- Efficient series production - Faster and more cost-effective than open-die forging.
- Low material loss - Less waste than with other processes.
- Complex geometries possible - Ideal for automotive, aerospace and mechanical engineering.
- Good surface quality - Reduces the need for reworking.
Die forging is particularly advantageous for series production, complex components and high mechanical strength. Compared to open die forging, it offers higher precision, less reworking and more efficient material utilization, while being more flexible for different geometries compared to roll forging.
Despite many advantages, drop forging also has some limitations and disadvantages:
- High tooling costs - Only worthwhile for large series.
- Limited geometries - Very complex or large parts are difficult to produce.
- Loss of material - burr formation requires reworking.
- High energy requirement - Forging presses consume a lot of energy.
- Material limitations - Not all materials are easy to forge.
Drop forging is ideal for mass-produced, heavy-duty components, but high tooling costs and geometric limitations make it less suitable for small batches or custom-made products.